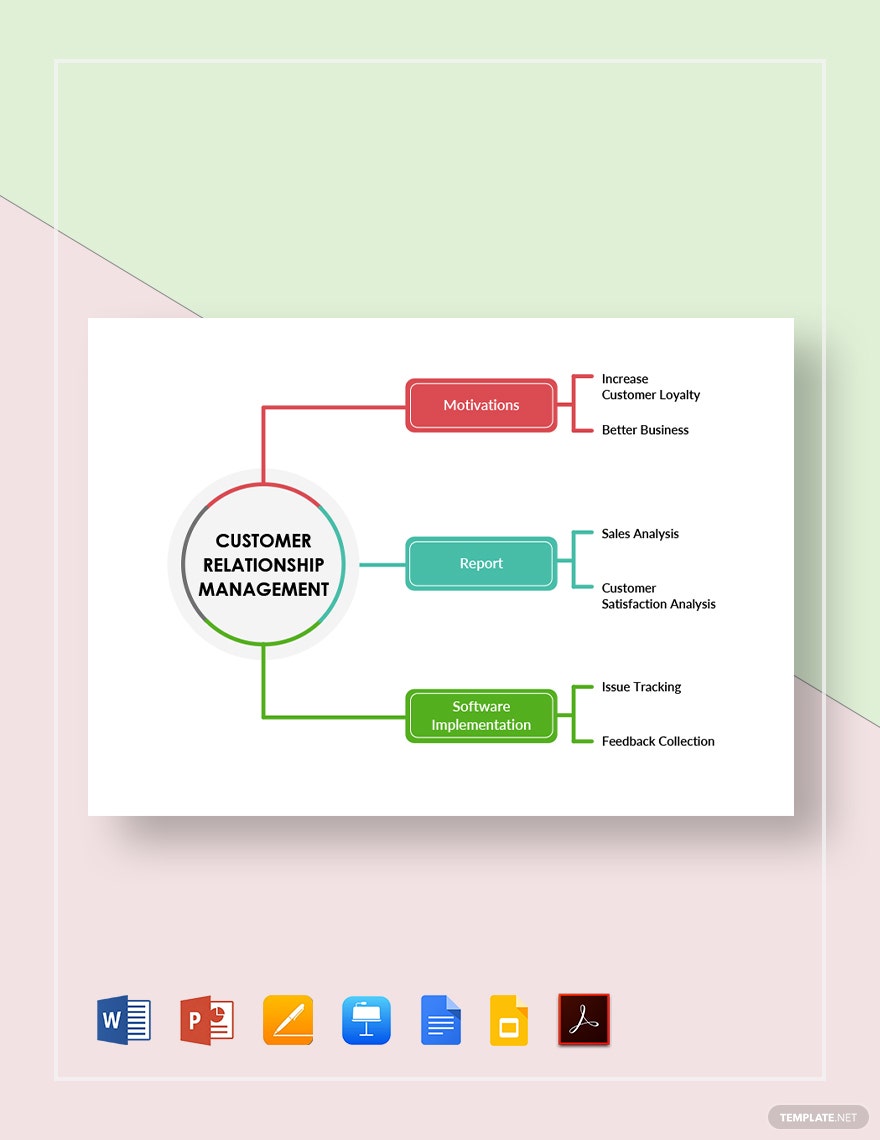
Group factors are a major factor in any organization's change. These can include both informal and formal groups within an organisation. While formal groups, like trade unions and other organizations, can resist change, informal groups can also be strong barriers to change. Changing group dynamics can change work flows, job design, social organisation, and influence systems. Changes can also impact communication patterns and status systems. Understanding these factors and how to deal with them will be crucial in successfully implementing any change.
Organizational resistance to change
The reason for the resistance to change in an organisation is usually down to how the people perceive the change. According to Mullin, there is little that management can do to address this problem. But there are ways to solve this problem. There are two ways employees can approach the issue of organisational changes. The first is that employees respond to changes based on how they perceive them. Van Tonder's view is different. It suggests that employees form their responses to organizational change.
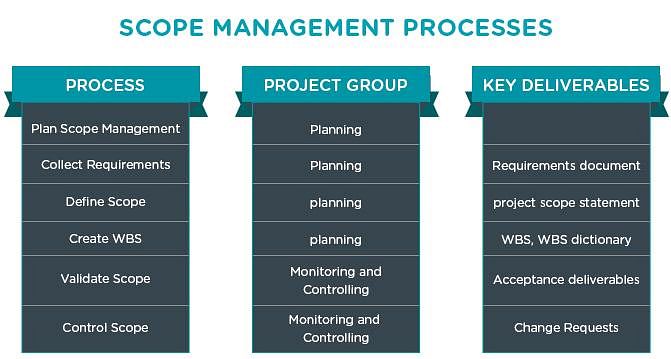
Types and types of organizational change
Organizations go through many types of changes, from complete transformations to structural changes. Companies must adapt to keep up with the constantly changing business environment. Adaptive Change is not often disruptive. Instead, it occurs when an organization strives to improve processes and strategies. Organisations that undergo transformations should plan for the transition period, and prepare properly. This article will explain the main differences between types of change and how they could affect an organization.
Influence of external environments
External environment can be a complex web of factors that impact the performance of an organisation. These factors do not have a fixed pattern and change at different rates. Instead, they are mutually reinforcing and influence one another. Changes in the environment force organizations to adapt and make pro-active changes. This article will address some of the common factors that can affect external environment change. It is important that you understand the interconnectedness among the external and internal environments of your company.
Process-oriented changes
Changes that impact workflow, productivity and group cohesion are called process-oriented changes in an organization. Process-oriented change can be seen in robotics in manufacturing plants as well as laser scanning checkout systems at supermarkets. Both types can have a different impact on an organisation's culture. It is important to consider the culture within which your company operates. This article will talk about the benefits of process-oriented changes and the various types of organizational change that are possible.
Structural Change
Organisational development requires change management. Small changes to policies or tools can have an impact on a business. But large-scale transformations have the potential of transforming a company. The strategy chosen is crucial to the success of such transformations. To make a change successful, you need to plan and prepare well. The ultimate goal should be identified, and a plan developed to reach it. Change management is a continuous process that should be carried out to ensure the success of the new strategy.
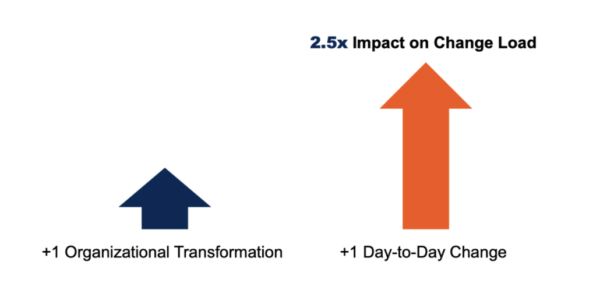
Technological Change
Technology change management is a process of identifying new technologies that can be beneficial for an organisation. Technology change management involves planning and defining requirements, estimating benefits and life spans, identifying appropriate technology sources, and documenting the results. Documenting the process of selecting technologies for an organisation is called a technology management policy and procedure. The process documents all possible solutions and challenges, as well acquisitions of new technology and requests.
FAQ
What are the steps in the decision-making process in management?
Managers have to make complex decisions. This involves many factors including analysis, strategy and planning, implementation, measurement and evaluation, feedback, feedback, and others.
It is important to remember that people are human beings, just like you. They make mistakes. There is always room to improve, especially if your first priority is to yourself.
This video explains the process of decision-making in Management. We discuss different types of decisions as well as why they are important and how managers can navigate them. The following topics will be covered.
What role does a manager have in a company's success?
Each industry has a different role for a manager.
The manager oversees the day-to-day activities of a company.
He/she makes sure that the company meets its financial obligations, and that it produces goods or services that customers desire.
He/she ensures employees adhere to all regulations and quality standards.
He/she plans and oversees marketing campaigns.
What is Six Sigma, exactly?
This is a method of quality improvement that emphasizes customer service, continuous learning, and customer service. It is a method that eliminates defects using statistical techniques.
Six Sigma was developed at Motorola in 1986 as part of its efforts to improve manufacturing processes.
This idea quickly spread throughout the industry. Today, many organizations use six sigma methods for product design, production and delivery.
It seems so difficult sometimes to make sound business decisions.
Businesses are complex systems, and they have many moving parts. People who manage them have to balance multiple priorities while dealing with complexity and uncertainty.
To make good decisions, you must understand how these factors affect the entire system.
To do this, you must think carefully about what each part of the system does and why. Next, consider how each piece interacts with the others.
It is also worth asking yourself if you have any unspoken assumptions about how you have been doing things. If you don't have any, it may be time to revisit them.
For help, ask someone else if you're still stumped after all the above. They might have different perspectives than you, and could offer insight that could help you solve your problem.
What does "project management" mean?
We mean managing the activities involved in carrying out a project.
We include defining the scope of the project, identifying the requirements, preparing the budget, organizing the project team, scheduling the work, monitoring progress, evaluating results, and closing down the project.
Statistics
- UpCounsel accepts only the top 5 percent of lawyers on its site. (upcounsel.com)
- The profession is expected to grow 7% by 2028, a bit faster than the national average. (wgu.edu)
- As of 2020, personal bankers or tellers make an average of $32,620 per year, according to the BLS. (wgu.edu)
- Your choice in Step 5 may very likely be the same or similar to the alternative you placed at the top of your list at the end of Step 4. (umassd.edu)
- Our program is 100% engineered for your success. (online.uc.edu)
External Links
How To
How can you implement the Kaizen technique?
Kaizen means continuous improvement. The term was coined in the 1950s at Toyota Motor Corporation and refers to the Japanese philosophy emphasizing constant improvement through small incremental changes. It's a process where people work together to improve their processes continuously.
Kaizen is one method that Lean Manufacturing uses to its greatest advantage. Employees responsible for the production line should identify potential problems in the manufacturing process and work together to resolve them. This way, the quality of products increases, and the cost decreases.
Kaizen is an approach to making every worker aware and alert to what is happening around them. It is important to correct any problems immediately if they are discovered. Report any problem you see at work to your manager.
Kaizen is based on a few principles. Always start with the end product in mind and work our way back to the beginning. We can improve the factory by first fixing the machines that make it. Next, we fix the machines which produce components. Finally, we repair the workers who are directly involved with these machines.
This is known as "kaizen", because it emphasizes improving each step. When we are done fixing the whole factory, we go back to the beginning and continue until we reach perfection.
It is important to understand how to measure the effectiveness and implementation of kaizen in your company. There are many ways you can determine if kaizen has been implemented well. One of these ways is to check the number of defects found on the finished products. Another way is to see how much productivity has increased since implementing kaizen.
If you want to find out if your kaizen is actually working, ask yourself why. Did you do it because it was legal or to save money? Did you really believe that it would be a success factor?
If you answered yes to any one of these questions, congratulations! You're now ready to get started with kaizen.