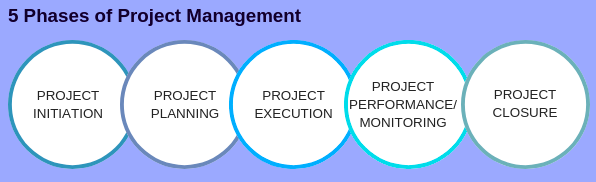
Value at Risk is a way to estimate the risk of investing. This calculation usually estimates the potential loss of an investment in one day. However, it can also take into account other factors, such as the market's volatility. This calculation is essential for all investors in stocks or bonds. This calculation can help you determine which investments are best for you, based on your risk tolerances and goals. You can also use the value-at-risk calculation to plan your retirement strategy.
Probability of losing a specific amount depends on how much money is being risked
We use probabilities to predict the likelihood of our investment success. A $10,000 investment in stocks would result in a 12% loss of that money. Peril is the amount of money you lose in case your investment fails. As an example, suppose we lose $5,000 on a investment. The damage would be $4000. It is important to note that probability does not guarantee a successful outcome.
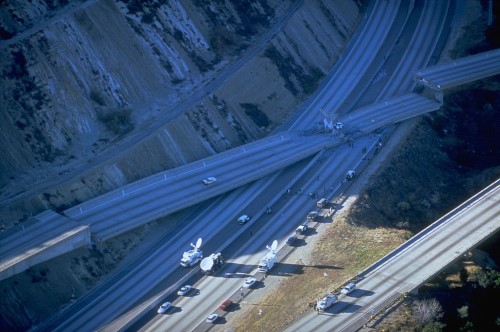
Calculation of VaR
When you invest, value at risk is an important tool that you should use to determine the amount of risk involved with a given investment. Value at risk measures the probability of losing money based on the past performance of the investment. It also takes current market conditions into account. This calculation can be used for calculating the average loss within a portfolio. The calculation for value at risk is simple. The percentage value of a portfolio equals the expected loss in 5%.
Monte Carlo method
The Monte Carlo approach is used often in financial risk management. It is flexible and adaptable, and it can handle a variety scenarios. This makes it one of the most effective VAR methods. Simulations can be used to account for complex pricing patterns as well as nonlinear exposures. This method can also be used to develop more complicated models and measure risk. There are however limitations to this method.
Historical method
Popular in investing is the Historical method of Value at Risk (VaR). It uses historical data in order to determine risk factors. Then, it applies that information to current market prices. It is easy to use and intuitive to calculate VaR. The value corresponds with a maximum loss within a certain period. Important to remember that VaR calculations are only as accurate as the correct data points they use. It is important to capture changes in market dynamics such as a major financial crisis, to ensure that it is accurate.
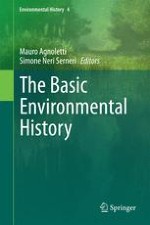
The VaR's effect on liquidity
Valuation at risk (or VaR) is a measure for the asset's riskiness. It is defined as the difference between the asset's present value and the future expected value. This measure of risk is most used by financial institutions. The mathematical model used to calculate the concept focuses on rare events. The risk distribution of the event is parametric. It has the mean at the middle and low tails at the bottom. In the FTSE, there are five such days within a 25 years period.
FAQ
What is Six Sigma?
It is a way to improve quality that places emphasis on customer service and continuous learning. The goal is to eradicate defects through statistical techniques.
Motorola's 1986 efforts to improve manufacturing process efficiency led to the creation of Six Sigma.
The idea spread quickly in the industry. Today many organizations use six-sigma techniques to improve product design.
What is the main difference between Six Sigma Six Sigma TQM and Six Sigma Six Sigma?
The main difference between these two quality-management tools is that six-sigma concentrates on eliminating defects while total QM (TQM), focuses upon improving processes and reducing expenses.
Six Sigma is an approach for continuous improvement. This approach emphasizes eliminating defects through statistical methods like control charts, Pareto analysis, and p-charts.
This method has the goal to reduce variation of product output. This is accomplished through identifying and correcting root causes.
Total quality management is the measurement and monitoring of all aspects within an organization. It also includes the training of employees to improve performance.
It is commonly used as a strategy for increasing productivity.
What are management concepts?
Management concepts are the practices and principles managers use to manage people or resources. They include such topics as human resource policies, job descriptions, performance evaluations, training programs, employee motivation, compensation systems, organizational structure, and many others.
It seems so difficult sometimes to make sound business decisions.
Complex systems and many moving parts make up businesses. They require people to manage multiple priorities and deal with uncertainty and complexity.
Understanding how these factors impact the whole system is key to making informed decisions.
You must first consider what each piece of the system does and why. It is important to then consider how the individual pieces relate to each other.
You should also ask yourself if there are any hidden assumptions behind how you've been doing things. If not, you might want to revisit them.
You can always ask someone for help if you still have questions after all of this. They may see things differently from you and have insights that could help you find a solution.
Six Sigma is so popular.
Six Sigma is easy to implement and can produce significant results. It can also be used to help companies identify and focus on the most important aspects of their business.
What are the three basic management styles?
There are three types of management: participative, laissez faire, and authoritarian. Each style is unique and has its strengths as well as weaknesses. Which style do yo prefer? Why?
Authoritarian – The leader sets a direction and expects everyone follows it. This style works well if an organization is large and stable.
Laissez faire - Each individual can decide for himself/herself. This style is best when the organization has a small but dynamic group.
Participative: The leader listens to everyone's ideas and suggestions. This is a great style for smaller organizations that value everyone.
Statistics
- The BLS says that financial services jobs like banking are expected to grow 4% by 2030, about as fast as the national average. (wgu.edu)
- The profession is expected to grow 7% by 2028, a bit faster than the national average. (wgu.edu)
- The average salary for financial advisors in 2021 is around $60,000 per year, with the top 10% of the profession making more than $111,000 per year. (wgu.edu)
- Hire the top business lawyers and save up to 60% on legal fees (upcounsel.com)
- 100% of the courses are offered online, and no campus visits are required — a big time-saver for you. (online.uc.edu)
External Links
How To
How do I do the Kaizen Method?
Kaizen means continuous improvement. The Japanese philosophy emphasizes small, incremental improvements to achieve continuous improvement. This term was created by Toyota Motor Corporation in 1950. This is a collaborative process in which people work together to improve their processes continually.
Kaizen is one of the most effective methods used in Lean Manufacturing. Employees responsible for the production line should identify potential problems in the manufacturing process and work together to resolve them. This increases the quality of products and reduces the cost.
Kaizen is about making everyone aware of the world around them. So that there is no problem, you should immediately correct it if something goes wrong. If someone is aware of a problem at work, he/she should inform his/her manager immediately.
Kaizen is based on a few principles. Start with the end product, and then move to the beginning. We can improve the factory by first fixing the machines that make it. We then fix the machines producing components, and the machines producing raw materials. Then, we fix those who work directly with the machines.
This method, called 'kaizen', focuses on improving each and every step of the process. After we're done with the factory, it's time to go back and fix the problem.
To implement kaizen in your business, you need to find out how to measure its effectiveness. There are many ways to tell if kaizen is effective. One way is to examine the amount of defects on the final products. Another way is determining how much productivity increased after implementing kaizen.
To determine if kaizen is effective, you should ask yourself why you chose to implement kaizen. Was it just because it was the law or because you wanted to save money? Did you really believe it would lead to success?
If you answered yes to any one of these questions, congratulations! You are now ready to begin kaizen.