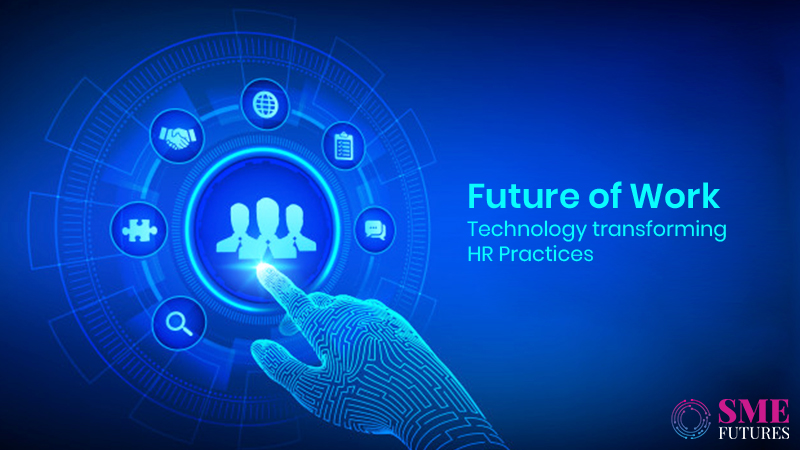
Planning involves a series of activities that includes setting goals, objectives and taking action. It is about what should happen and how. This is how you define the objectives and means of an activity or project. It involves the identification of a course or action, as well as identifying resources and how to accomplish it. A well-planned plan is essential to any successful project or organisation. Here are some ideas for planning.
Plan
Simply put, planning is the process by which an organization determines its goals. It can also be used to help you make decisions about when and how best to proceed to reach your goals. There are many types of plans, and the type of plan that is right for your organization is determined by the type of organization and its needs. Some plans are specific and detailed, while others have more flexibility and can be altered over time.
Planning is the act of anticipating the future and choosing the best course. It involves thinking ahead, analyzing data, and evaluating alternatives before taking action. This involves the process of defining the objectives for a project/business and linking them with business opportunities. It is an integral part that involves problem solving. These are just a few examples of how planning can help organizations achieve their goals.
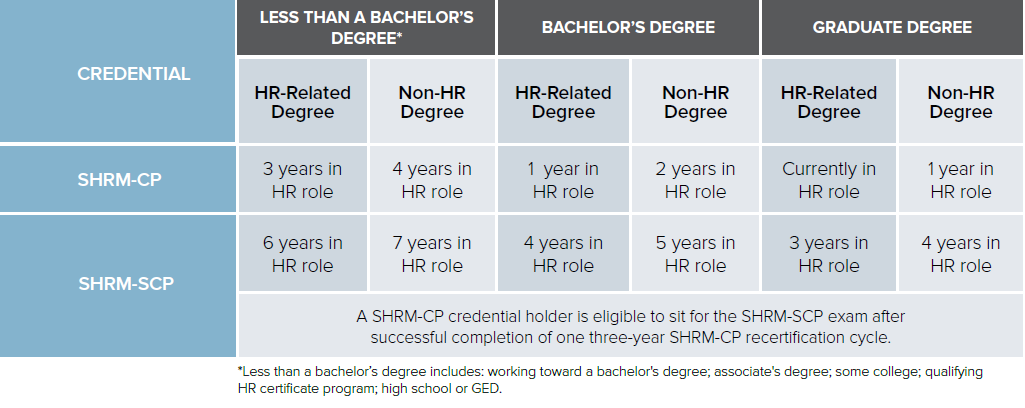
Organize
Organizational planning helps companies to achieve their goals and respond quickly to changes in the workplace. It helps to clarify expectations, roles and responsibilities. It helps companies respond to changes in the workplace and achieve more success than they would without it. An organizational planning software program is a good way to get started. These are just a few of the best features in an organizational planning program. These features make your work much easier and more effective. Learn how organizational planning will help you company succeed.
Planning involves organizing. It involves determining the situation, making decisions and then taking action. It involves setting priorities, creating complex plans and achieving a goal. It is an essential part management. This will ensure effectiveness and efficiency. Once you have created a plan, organize it to make it as efficient as possible. Your organization will achieve its objectives by organizing and delivering on its mandate.
Decide on course of action
A plan is a process of determining the best course of action. The process of planning entails considering different options and determining what will be best. For the benefit of the organization, a plan must be accurate. This is an essential part of project management. These three tips will help you determine the best course. Create a plan that outlines your goals and objectives. Once you've made a plan you can implement it correctly.
Determine your resources
Project planning begins with determining the resources. It is essential to know the available resources and how you plan to use them in order for a project to be successful. The first step in defining resources is to gather the tasks that need to be accomplished. This can be done on a Gantt chart or task list, with estimated start and end dates. Next, you will need to decide which resources are required to complete these tasks. These must then be input into your planning tool.
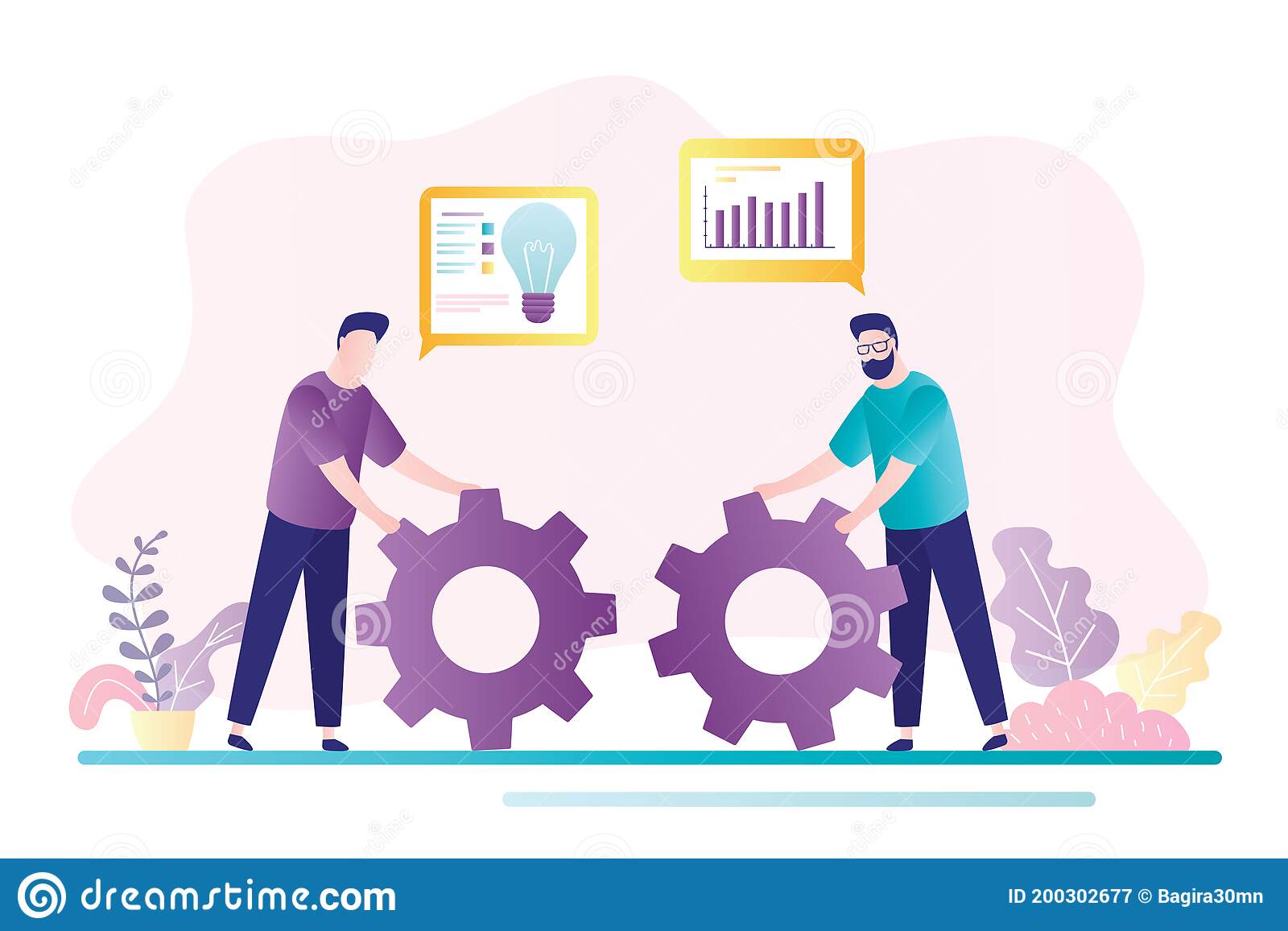
Planning your resource needs is essential. Your project will not succeed if you don’t know how many resources you will require. A project task list can help you determine how many resources you will need. This can make hiring easier. This type of planning is also useful for keeping track of the time and resources that are required for each task. For instance, a large project may require several team members working overtime to complete all the tasks.
FAQ
What is the difference between a project and a program?
A project is temporary while a programme is permanent.
A project usually has a specific goal and deadline.
It is usually done by a group that reports back to another person.
A program typically has a set goal and objective.
It is usually implemented by a single person.
How does a manager learn to manage?
Through demonstrating good management skills at every opportunity
Managers need to monitor their subordinates' performance.
It is important to take immediate action if your subordinate doesn't perform as expected.
You must be able to spot what is lacking and how you can improve it.
What is TQM and how can it help you?
The industrial revolution was when companies realized that they couldn't compete on price alone. This is what sparked the quality movement. If they wanted to stay competitive, they needed to improve their quality and efficiency.
To address this need for improvement management created Total Quality Management (TQM) which aimed to improve all aspects of an organization's performance. It included continuous improvement, employee involvement and customer satisfaction.
What is Kaizen?
Kaizen is a Japanese term meaning "continuous improvement." It is a philosophy that encourages employees to constantly look for ways to improve their work environment.
Kaizen is founded on the belief of everyone being able to do their job well.
Why is it so hard to make smart business decisions?
Complex systems and many moving parts make up businesses. People who manage them have to balance multiple priorities while dealing with complexity and uncertainty.
Understanding the impact of these factors on the system is crucial to making sound decisions.
This requires you to think about the purpose and function of each component. You then need to consider how those individual pieces interact with each other.
It is also worth asking yourself if you have any unspoken assumptions about how you have been doing things. If you don't have any, it may be time to revisit them.
If you're still stuck after all this, try asking someone else for help. You might find their perspective is different from yours and they may have insight that can help you find the solution.
Statistics
- The average salary for financial advisors in 2021 is around $60,000 per year, with the top 10% of the profession making more than $111,000 per year. (wgu.edu)
- As of 2020, personal bankers or tellers make an average of $32,620 per year, according to the BLS. (wgu.edu)
- Hire the top business lawyers and save up to 60% on legal fees (upcounsel.com)
- This field is expected to grow about 7% by 2028, a bit faster than the national average for job growth. (wgu.edu)
- Your choice in Step 5 may very likely be the same or similar to the alternative you placed at the top of your list at the end of Step 4. (umassd.edu)
External Links
How To
How is Lean Manufacturing done?
Lean Manufacturing techniques are used to reduce waste while increasing efficiency by using structured methods. These processes were created by Toyota Motor Corporation, Japan in the 1980s. It was designed to produce high-quality products at lower prices while maintaining their quality. Lean manufacturing seeks to eliminate unnecessary steps and activities in the production process. It is made up of five elements: continuous improvement, continuous improvement, just in-time, continuous change, and 5S. Pull systems involve producing only what the customer wants without any extra work. Continuous improvement is the continuous improvement of existing processes. Just-in-time refers to when components and materials are delivered directly to the point where they are needed. Kaizen is continuous improvement. This can be achieved by making small, incremental changes every day. The 5S acronym stands for sort in order, shine standardize and maintain. These five elements are combined to give you the best possible results.
Lean Production System
Six key concepts underlie the lean production system.
-
Flow - focus on moving material and information as close to customers as possible;
-
Value stream mapping is the ability to divide a process into smaller tasks, and then create a flowchart that shows the entire process.
-
Five S's – Sort, Put In Order Shine, Standardize and Sustain
-
Kanban - visual cues such as stickers or colored tape can be used to track inventory.
-
Theory of Constraints - Identify bottlenecks in the process, and eliminate them using lean tools such kanban boards.
-
Just-in Time - Send components and material directly to the point-of-use;
-
Continuous improvement - make incremental improvements to the process rather than overhauling it all at once.