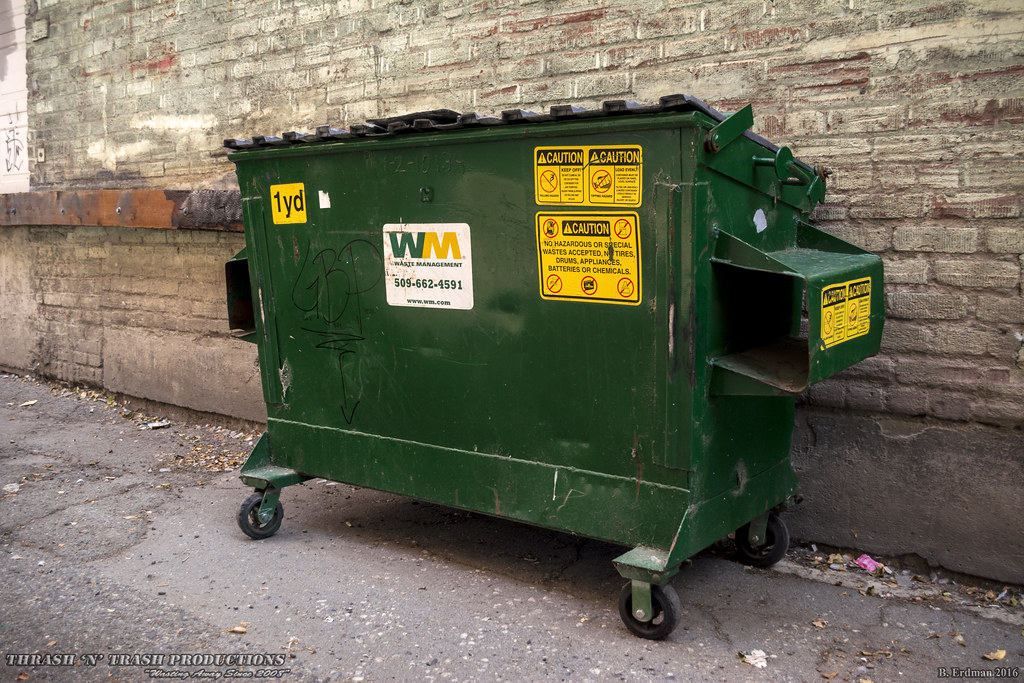
Your employees' well-being is dependent on a positive workplace environment. It promotes better productivity, decreases burnout, and reduces complaints. Studies have shown that motivated and happy employees perform better. Before creating a positive environment for your employees, there are several things you need to consider.
Positive work environments are conducive to productivity
A positive work environment creates a calm atmosphere that allows people to focus on their work and be more productive. It is conducive to cognitive and physical well being, and often includes clear communication between the employees and the management. This type environment encourages employees to learn and grow by offering them opportunities to ask questions as well as constructive feedback.
Positive workplace environments encourage employees to put in 200%. They don't hesitate to accept responsibility and won't play petty revenge when they are given negative feedback. It promotes teamwork and camaraderie. It encourages employees take breaks and enjoy the work they do.
Employees feel happier
It is possible to create a positive work environment that makes your employees happy. Employees who are happy at their job are more productive and are more likely sharing their ideas with others. They are also less likely to be sick and feel less stressed.
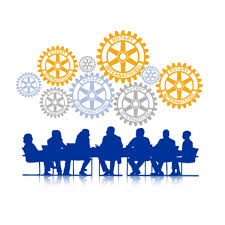
University of Birmingham research has shown that positive working environments can increase employee happiness. Employees who are happy work better, do more calls-to-sales conversions per hour and follow their work schedule.
Burnout can be reduced
A burnout strategy can be a risk to an organization's productivity and health. Burnout can affect working relationships and is a psychosocial condition. It can be characterized as a lack in empathy and emotional disconnect from patients and coworkers. Research has shown that proactive measures, such as creating a positive work environment, can prevent this condition.
Positive work environments can help reduce burnout by increasing individual and team efficacy. Empowerment helps increase individual efficacy. It also buffers the effects of exhaustion from cynicism. Personal efficacy is directly related to team effectiveness. Communication among staff members improves the quality of their communication.
It decreases complaints
Employees feel better about their work when they are part of a positive workplace. A positive work environment is more conducive to employees staying focused on their tasks and completing them on time. They are also more productive, and they have higher employee status. Positive working environments promote collaboration. It allows employees to express their ideas and receive feedback to improve their performance.
Employers will be less likely to complain if they have a positive environment. The first step in creating a positive working environment is to eliminate harassment, bullying and discrimination. It is great to work in a workplace free from harassment and discrimination. Positive work environments are good for employee morale, decrease complaints, and lower employee stress.
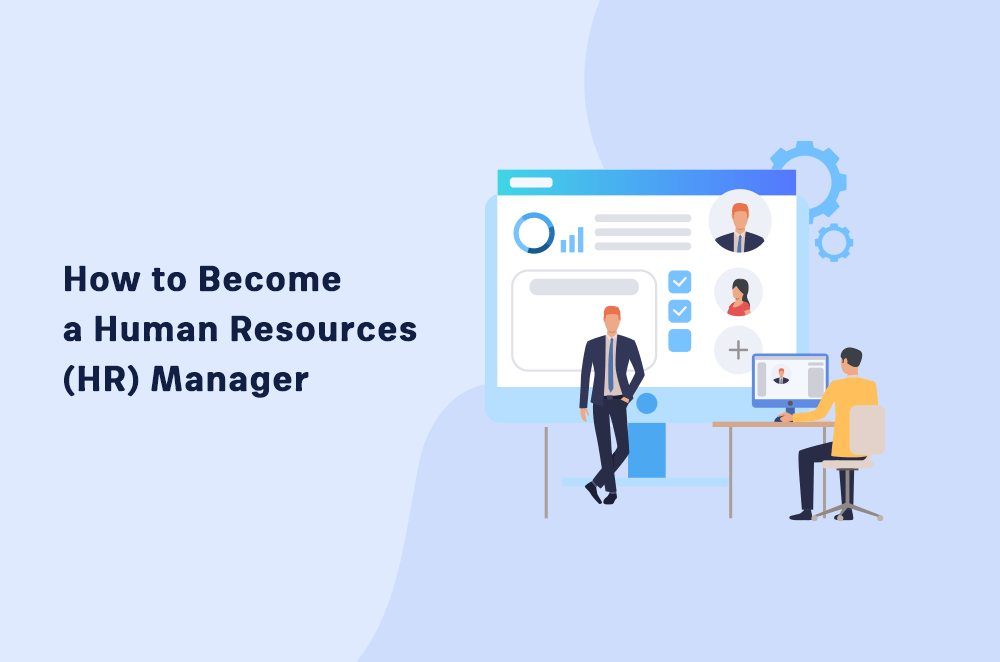
It helps teachers feel better
The teacher's workplace environment can affect their well-being. There are many ways to improve teacher wellness, including providing a supportive environment for staff and hosting regular meetings. A school audit can help teachers assess their health and set goals to improve.
Teachers are exposed to a thousand different interactions every day, and the quality of those interactions is critical to their well-being. Studies show that teachers can suffer from poor wellbeing if they are exposed to a toxic culture. Positive environments support healthy practice and help teachers focus on their students. Professional development is essential for teachers. Teachers want PD to improve teacher wellbeing. This is according to a survey.
FAQ
How does a manager learn to manage?
Through demonstrating good management skills at every opportunity
Managers must monitor the performance of subordinates constantly.
It is important to take immediate action if your subordinate doesn't perform as expected.
You must be able to spot what is lacking and how you can improve it.
What is TQM, exactly?
The industrial revolution led to the birth and growth of the quality movement. Manufacturing companies realized they couldn't compete solely on price. They had to improve efficiency and quality if they were to remain competitive.
To address this need for improvement management created Total Quality Management (TQM) which aimed to improve all aspects of an organization's performance. It included continuous improvement processes, employee involvement, and customer satisfaction.
What is Kaizen?
Kaizen is a Japanese term which means "continuous improvement." This philosophy encourages employees to continually look for ways to improve the work environment.
Kaizen is founded on the belief of everyone being able to do their job well.
Statistics
- The average salary for financial advisors in 2021 is around $60,000 per year, with the top 10% of the profession making more than $111,000 per year. (wgu.edu)
- The profession is expected to grow 7% by 2028, a bit faster than the national average. (wgu.edu)
- As of 2020, personal bankers or tellers make an average of $32,620 per year, according to the BLS. (wgu.edu)
- Hire the top business lawyers and save up to 60% on legal fees (upcounsel.com)
- This field is expected to grow about 7% by 2028, a bit faster than the national average for job growth. (wgu.edu)
External Links
How To
How does Lean Manufacturing work?
Lean Manufacturing uses structured methods to reduce waste, increase efficiency and reduce waste. These processes were created by Toyota Motor Corporation, Japan in the 1980s. The primary goal was to make products with lower costs and maintain high quality. Lean manufacturing emphasizes removing unnecessary steps from the production process. It consists of five basic elements: pull systems, continuous improvement, just-in-time, kaizen (continuous change), and 5S. Pull systems allow customers to get exactly what they want without having to do extra work. Continuous improvement is constantly improving upon existing processes. Just-in time refers to components and materials being delivered right at the place they are needed. Kaizen means continuous improvement. Kaizen involves making small changes and improving continuously. Fifth, the 5S stand for sort, set up in order to shine, standardize, maintain, and standardize. These five elements can be combined to achieve the best possible results.
The Lean Production System
Six key concepts make up the lean manufacturing system.
-
Flow - The focus is on moving information and material as close as possible to customers.
-
Value stream mapping - break down each stage of a process into discrete tasks and create a flowchart of the entire process;
-
Five S's – Sort, Put In Order Shine, Standardize and Sustain
-
Kanban – visual signals like colored tape, stickers or other visual cues are used to keep track inventory.
-
Theory of constraints - identify bottlenecks during the process and eliminate them with lean tools like Kanban boards.
-
Just-intime - Order components and materials at your location right on the spot.
-
Continuous improvement - incremental improvements are made to the process, not a complete overhaul.