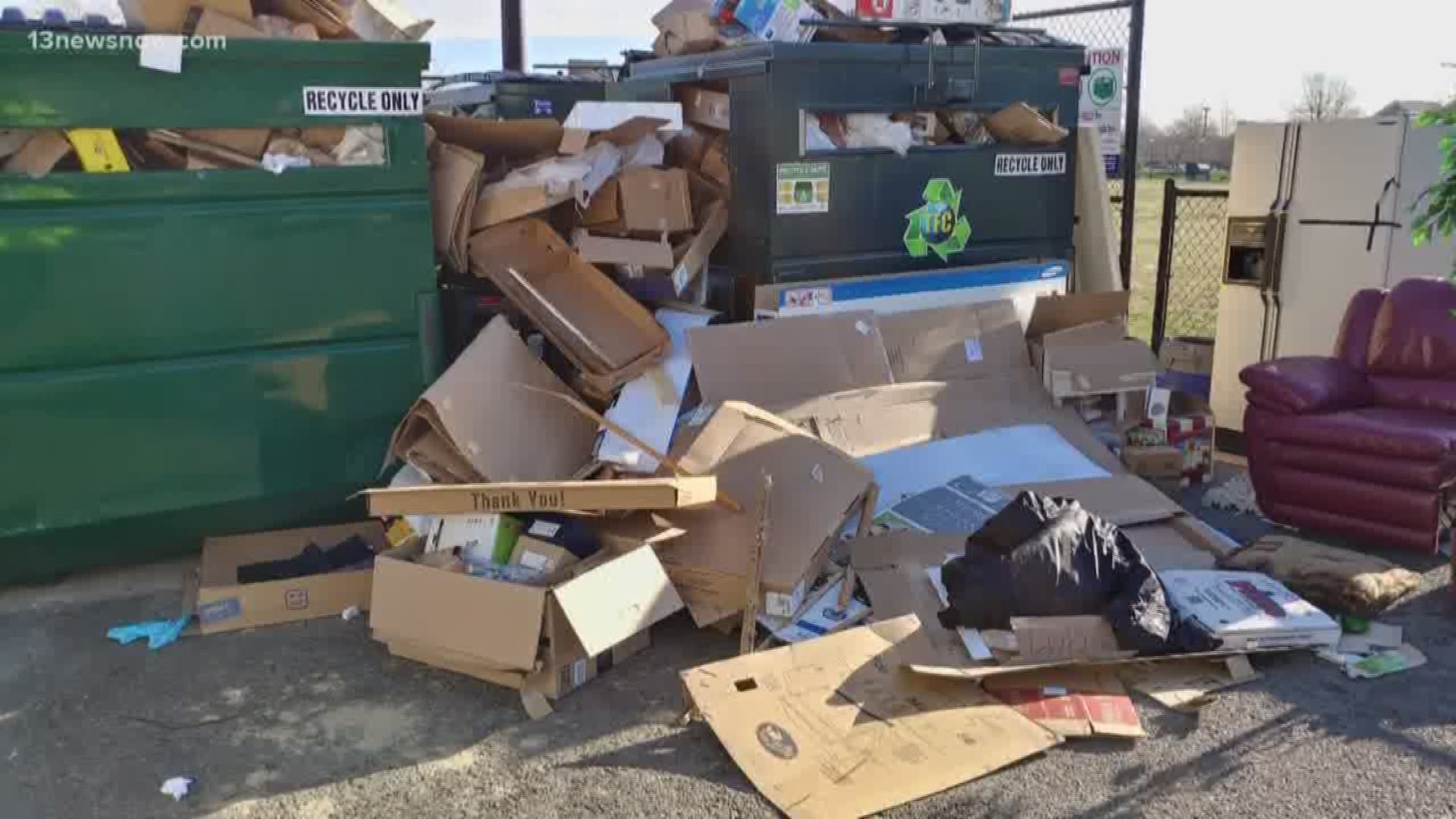
If you're a fan of clean environments, you've likely heard of Allied Waste Industries, Inc. The Fortune 500 company ran solid waste collection businesses as well as recycling facilities and landfills. This company was a leader in the United States' solid waste sector. In recent years, it has experienced several challenges that have pushed it to change its business model. Allied Waste has remained a viable and reliable company, offering convenient and clean services.
Allied Waste Industries, Inc.
Allied Waste Industries, Inc., a Fortune 500 firm, was headquartered in Phoenix, Arizona. It was a vertically integrated business that owned landfills and recycling facilities as well as solid waste collection firms. The company offered solid waste solutions and recycling services to businesses and cities in the United States. The company was a leader in solid waste for many years. But it closed its doors in 2012, and its employees are left with a big debt burden.
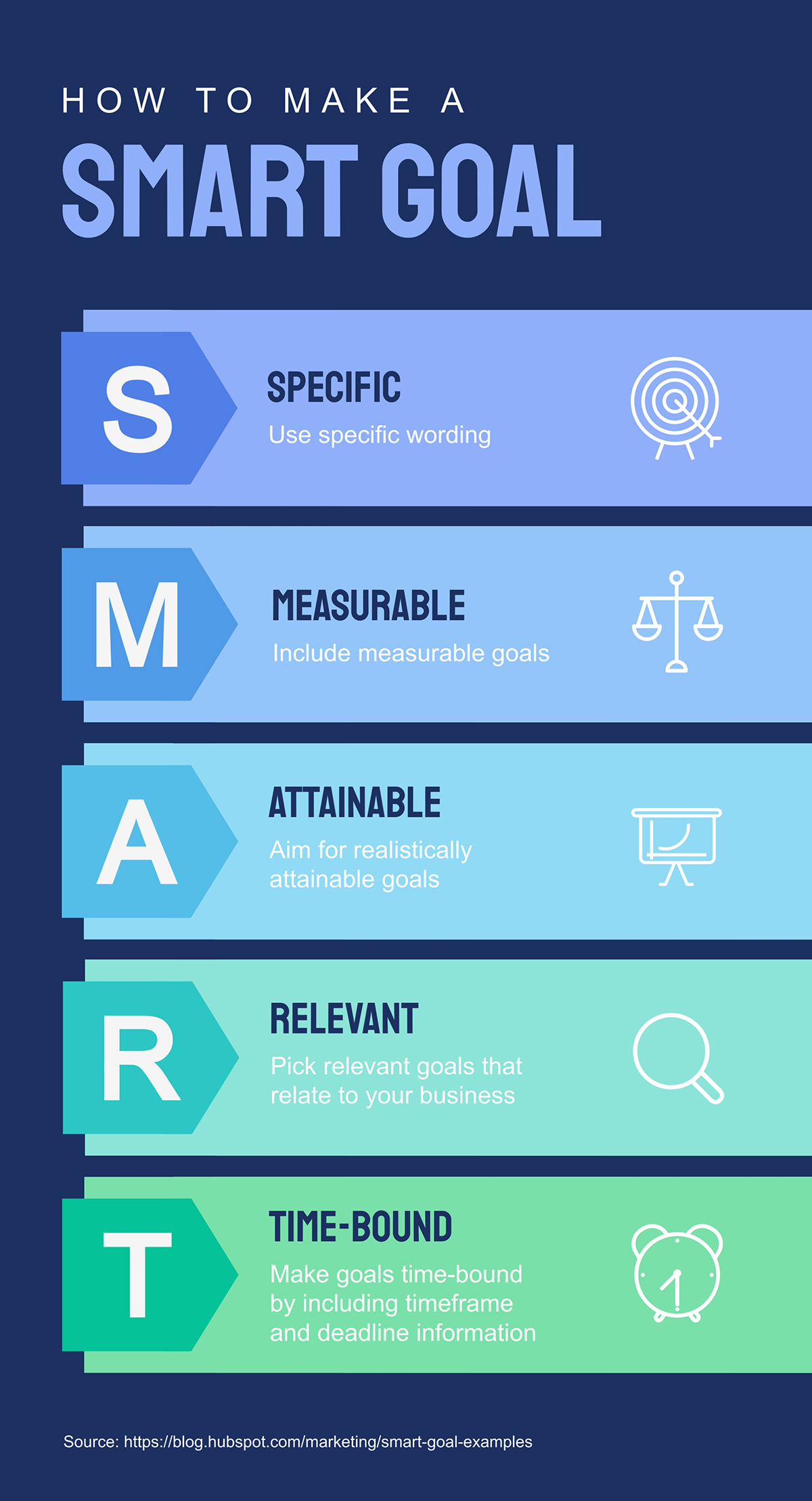
The company bought two Illinois-based waste companies in 1993. National Scavenger Service, Inc., operated landfills and transfer stations. The first company was National Scavenger Service, Inc. R.I8, the second company, was established in New Mexico as a waste company. After a few mergers and acquisitions, Allied Waste managed to expand into many other states. The company now ranks among the largest waste management firms in the world.
Lessey (and Ivan) were promoted to vice chairman and CFO of AWI after the acquisition. Ferreira was the first president of AWI, having 20 years of experience. Lessey resigned as president of AWI in October 1989, to return to the venture capital sector. Daniel J. Ivan, the new CEO, assumed control of AWI. Despite recent turmoil, the company continued its mergers and acquisitions program.
Allied Waste Landfill Holdings, Inc.
Allied Waste is an American firm that operates landfills throughout the United States. Bruce Lessey founded the business in 1987. After serving in Houston for many years, Lessey began purchasing companies that dealt with trash. In 1989, his business was facing financial problems. Roger Ramsey, who co-founded Browning-Ferris Industries, Inc., provided assistance. Houston Partners LP owned a small part of Allied Waste. Lessey stated that Ramsey brought with him the knowledge and experience from his own business to Allied Waste's board in August 1989.
Allied Waste has around 41,000 employees. The company is vertically integrated with a decentralized management system. Its subsidiaries run recycling plants and transfer stations. It is owned four private equity funds and serves more than 10 million clients in 39 states. It owns 355 collection businesses and 181 transfer station. It also owns 167 active landfills as well as 65 recycling facilities. Delaware is where the company's headquarters are located.
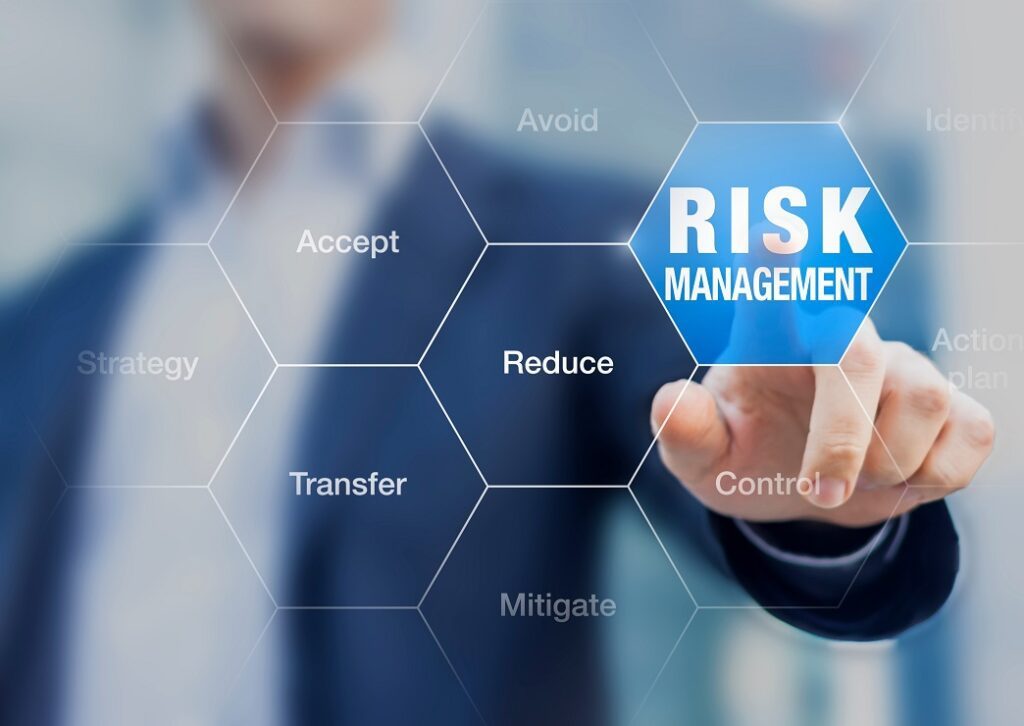
In 2002, it was the second-largest US solid waste disposal company. The company reported a profit for the first quarter 2002, as opposed to nearly $36million in 2001. To accommodate its rapid growth, Allied invested money in infrastructure upgrades. The company also increased its number of locations, from two to four regions to twelve and 58 district. Allied Waste's internalization rates grew to 67 percent in 2001.
FAQ
What are management concepts, you ask?
Management concepts are the principles and practices used by managers to manage people, resources. These topics include job descriptions, performance evaluations and training programs. They also cover human resource policies, job description, job descriptions, job descriptions, employee motivation, compensation systems, organizational structures, and many other topics.
Why is project management so important?
Project management techniques ensure that projects run smoothly while meeting deadlines.
This is due to the fact that most businesses rely heavily upon project work in order to produce goods, and services.
These projects must be managed efficiently and effectively by companies.
Companies that do not manage their projects effectively risk losing time, money, or reputation.
What is TQM?
The industrial revolution was when companies realized that they couldn't compete on price alone. This is what sparked the quality movement. If they wanted to stay competitive, they needed to improve their quality and efficiency.
Management responded to the need to improve, and developed Total Quality Management (TQM). This focused on improving every aspect of an organization’s performance. It included continuous improvement, employee involvement and customer satisfaction.
Statistics
- This field is expected to grow about 7% by 2028, a bit faster than the national average for job growth. (wgu.edu)
- The BLS says that financial services jobs like banking are expected to grow 4% by 2030, about as fast as the national average. (wgu.edu)
- 100% of the courses are offered online, and no campus visits are required — a big time-saver for you. (online.uc.edu)
- The profession is expected to grow 7% by 2028, a bit faster than the national average. (wgu.edu)
- Your choice in Step 5 may very likely be the same or similar to the alternative you placed at the top of your list at the end of Step 4. (umassd.edu)
External Links
How To
How can Lean Manufacturing be done?
Lean Manufacturing methods are used to reduce waste through structured processes. They were developed by Toyota Motor Corporation in Japan during the 1980s. The goal was to produce quality products at lower cost. Lean manufacturing is about eliminating redundant steps and activities from the manufacturing process. It is made up of five elements: continuous improvement, continuous improvement, just in-time, continuous change, and 5S. The production of only what the customer needs without extra work is called pull systems. Continuous improvement refers to continuously improving existing processes. Just-in-time refers to when components and materials are delivered directly to the point where they are needed. Kaizen is continuous improvement. This can be achieved by making small, incremental changes every day. The 5S acronym stands for sort in order, shine standardize and maintain. These five elements are combined to give you the best possible results.
Lean Production System
Six key concepts are the basis of lean production:
-
Flow: The goal is to move material and information as close as possible from customers.
-
Value stream mapping- This allows you to break down each step of a process and create a flowchart detailing the entire process.
-
Five S's – Sort, Put In Order Shine, Standardize and Sustain
-
Kanban is a visual system that uses visual cues like stickers, colored tape or stickers to keep track and monitor inventory.
-
Theory of constraints - identify bottlenecks in the process and eliminate them using lean tools like kanban boards;
-
Just-intime - Order components and materials at your location right on the spot.
-
Continuous improvement - incremental improvements are made to the process, not a complete overhaul.