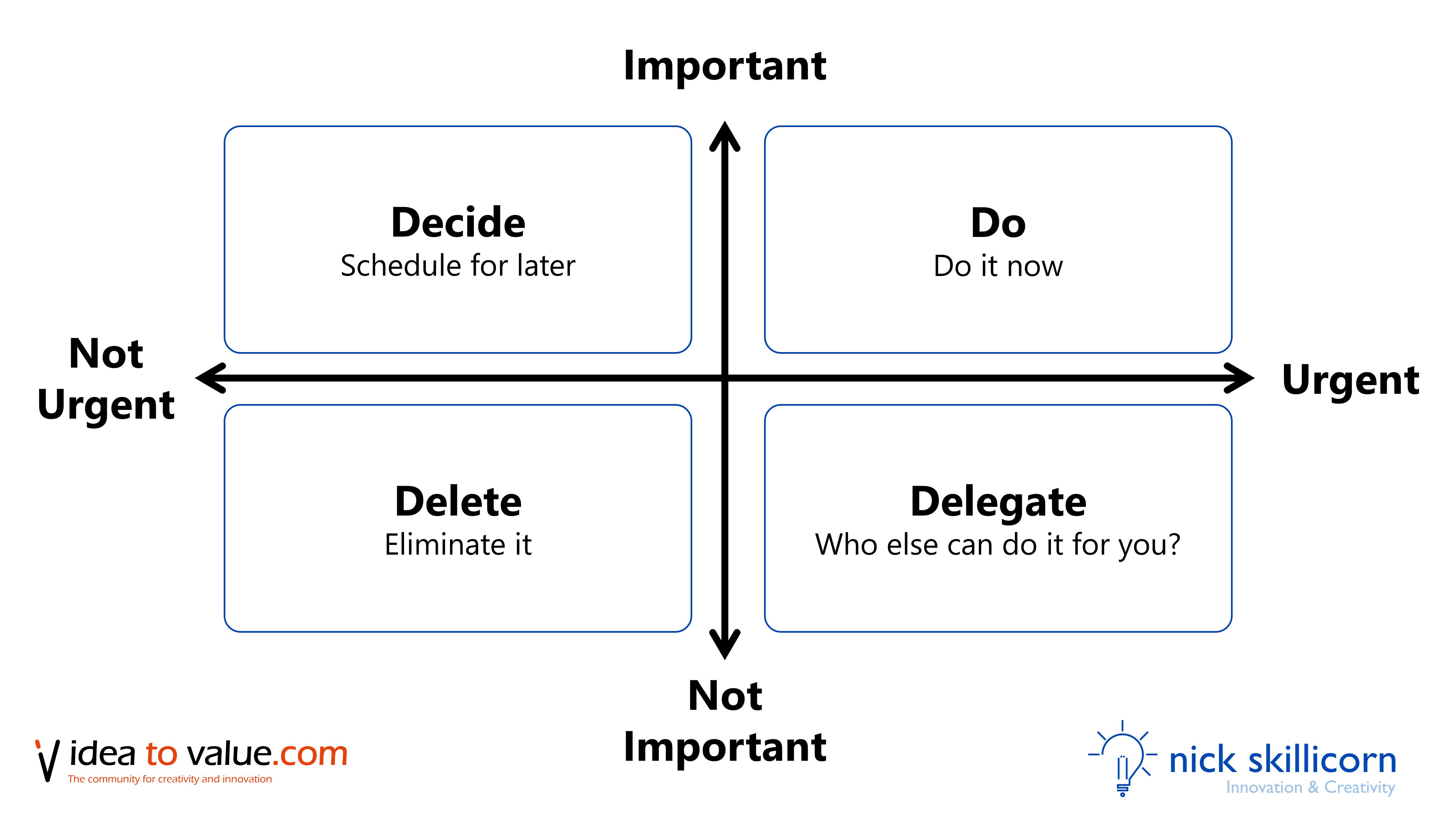
The hierarchy of control is an effective way to protect workers from hazards. It is widely used in many industries. This system is widely adopted and adopted by industry managers. However, this system can be modified in certain ways. Learn more by visiting our guide to NFPA70E hazard classified system and ARECC variation. This will allow you to more easily apply the hierarchy to your workplace.
NFPA70E
NFPA70E consists of a series of standards for workplace safety. In the 2018 edition, there is an Annex Q section. This describes human performance and human errors and their potential adverse consequences. This section includes a hierarchy that prioritizes the elimination and prevention of hazards. Electrical hazards require that you eliminate any source of electricity or hazards. Personal protective equipment should be used only as a last resort.
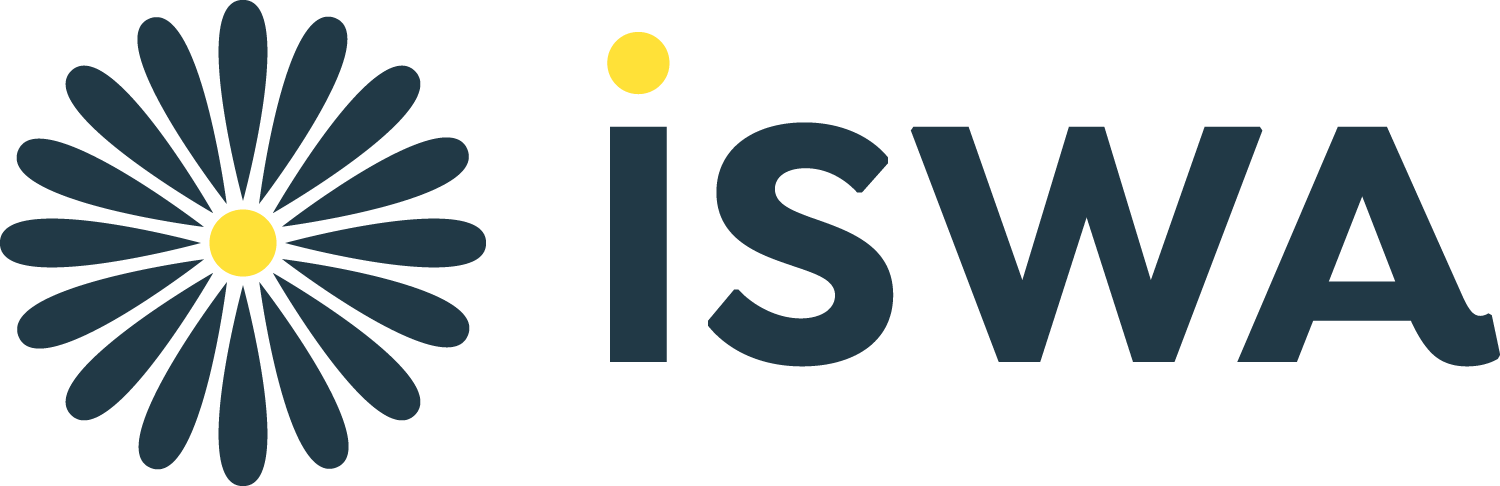
Next is to determine the degree of exposure to hazards. Then, you will need to decide on the most appropriate engineering controls that can reduce the severity. Engineering controls reduce the exposure to hazardous substances, but they cannot completely eliminate the hazard. The hierarchy of control's goal is to reduce the severity of hazards and prevent them from happening. An example of engineering control is a fog or vapor machine, ventilation system or fire alarm.
Appendices are also included in the NFPA 70E standard. These are documents that detail specific procedures and practices, and they provide guidance on how to do them. Appendices contain sample forms, PPE guidance and design requirements as well as risk assessment guidelines. Annexes provide information on how to implement the standard. Sometimes, annexes may be used to provide additional information that can help ensure safety in a workplace or building.
Variation of ARECC
The ARECC Variation in the Hierarchy of Control is a method of reducing the exposure to a given hazard. Although this system is a traditional one in the United States, Canada and other countries, it has been adapted to other countries. One example is that some countries prioritize isolation over engineering controls while others combine both. The ARECC variations include warnings and employee training. It is important to remember that warnings cannot eliminate all hazards at work.
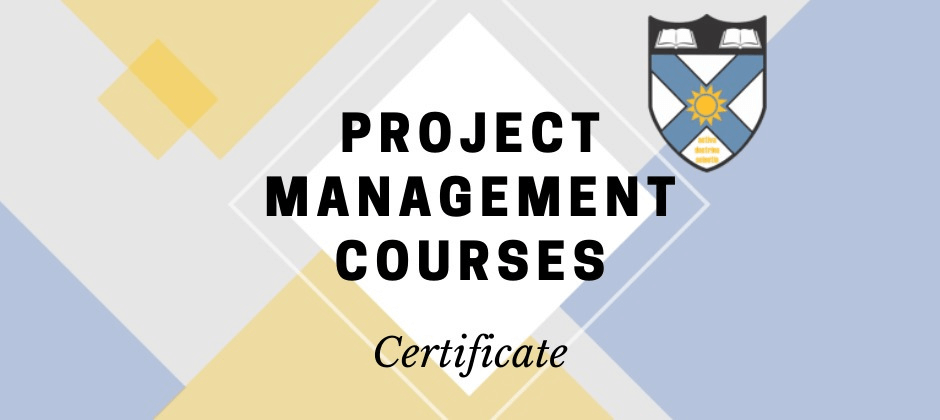
The ARECC hierarchy of controls is a framework for occupational safety and health. It helps to identify feasible solutions and ranks them according their effectiveness. The hierarchy contains five categories of controls: engineering controls and administrative controls. Each category has its own specific strengths and weaknesses, and is important for a specific situation. Some controls in the ARECC hierarchy work better than others.
FAQ
What are the steps of the management decision-making process?
The decision-making process for managers is complex and multifaceted. It involves many elements, including analysis, strategy. planning. implementation. measurement. evaluation. feedback.
It is important to remember that people are human beings, just like you. They make mistakes. As such, there is always room for improvement, especially if you're willing to put forth the effort to improve yourself first.
This video will explain how decision-making works in Management. We will explain the importance of different types decisions and how every manager can make them. You'll learn about the following topics:
How does Six Sigma work
Six Sigma employs statistical analysis to identify problems, measure them and analyze root causes. Six Sigma also uses experience to correct problems.
The first step to solving the problem is to identify it.
Next, data will be collected and analyzed to determine trends and patterns.
Next, corrective steps are taken to fix the problem.
Finally, data is reanalyzed to determine whether the problem has been eliminated.
This continues until the problem has been solved.
What are the 3 basic management styles?
There are three main management styles: participative, laissez-faire and authoritarian. Each style has its advantages and disadvantages. Which style do you prefer? Why?
Autoritarian – The leader sets the direction for everyone and expects them to follow. This style works well if an organization is large and stable.
Laissez-faire: The leader lets each person decide for themselves. This approach works best in small, dynamic organizations.
Participative – The leader listens and takes in ideas from all. This is a great style for smaller organizations that value everyone.
How do we build a culture that is successful in our company?
A culture of respect and value within a company is key to a productive culture.
It is founded on three basic principles:
-
Everybody has something to offer.
-
People are treated fairly
-
Respect is shared between individuals and groups
These values can be seen in the behavior of people. They will treat others with kindness and consideration.
They will listen respectfully to the opinions of others.
And they will encourage others to share ideas and feelings.
A company culture encourages collaboration and communication.
People feel safe to voice their opinions without fear of reprisal.
They understand that errors will be tolerated as long they are corrected honestly.
Finally, the company culture promotes honesty and integrity.
Everyone is aware that truth must be told.
Everyone understands there are rules that they must follow.
People don't expect special treatment or favors.
What role does a manager have in a company's success?
Managers' roles vary from industry to industry.
Managers generally oversee the day-today operations of a business.
He/she will ensure that the company fulfills its financial obligations.
He/she ensures employees adhere to all regulations and quality standards.
He/she plans new products and services and oversees marketing campaigns.
Statistics
- 100% of the courses are offered online, and no campus visits are required — a big time-saver for you. (online.uc.edu)
- The BLS says that financial services jobs like banking are expected to grow 4% by 2030, about as fast as the national average. (wgu.edu)
- Your choice in Step 5 may very likely be the same or similar to the alternative you placed at the top of your list at the end of Step 4. (umassd.edu)
- Our program is 100% engineered for your success. (online.uc.edu)
- As of 2020, personal bankers or tellers make an average of $32,620 per year, according to the BLS. (wgu.edu)
External Links
How To
What is Lean Manufacturing?
Lean Manufacturing techniques are used to reduce waste while increasing efficiency by using structured methods. They were created in Japan by Toyota Motor Corporation during the 1980s. The main goal was to produce products at lower costs while maintaining quality. Lean manufacturing seeks to eliminate unnecessary steps and activities in the production process. It is made up of five elements: continuous improvement, continuous improvement, just in-time, continuous change, and 5S. The production of only what the customer needs without extra work is called pull systems. Continuous improvement means continuously improving on existing processes. Just-in–time refers when components or materials are delivered immediately to their intended destination. Kaizen stands for continuous improvement. Kaizen can be described as a process of making small improvements continuously. The 5S acronym stands for sort in order, shine standardize and maintain. These five elements are used together to ensure the best possible results.
Lean Production System
The lean production system is based on six key concepts:
-
Flow: The goal is to move material and information as close as possible from customers.
-
Value stream mapping - Break down each stage in a process into distinct tasks and create an overview of the whole process.
-
Five S's – Sort, Put In Order Shine, Standardize and Sustain
-
Kanban - visual cues such as stickers or colored tape can be used to track inventory.
-
Theory of constraints: identify bottlenecks in your process and eliminate them using lean tools, such as kanban board.
-
Just-in Time - Send components and material directly to the point-of-use;
-
Continuous improvement - make incremental improvements to the process rather than overhauling it all at once.