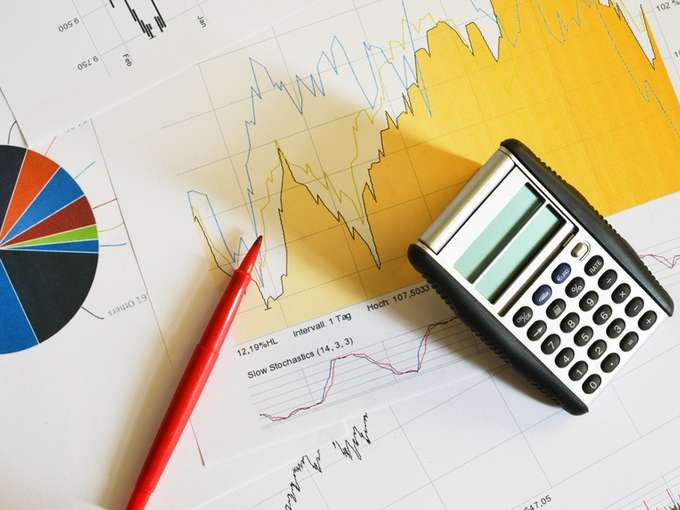
There are many factors to be aware of when dealing with construction waste. These include the types and disposal options for construction waste. There are also many regulations concerning the disposal and recycling of construction waste. This article will discuss hazardous waste and recycling. We will also discuss the importance of seperating hazardous waste from other waste. You'll be able to make responsible decisions regarding these materials once you have an in-depth understanding of each area.
Hazardous
Proper disposal of hazardous construction waste requires special equipment and expertise. These hazardous wastes can be dangerous to people and the environment if not treated properly. Also, improper disposal could result in fines from the authorities. Junk King and other waste removal companies are equipped to handle hazardous construction waste. Here are some examples of common construction wastes. These aren't all. Construction involves hazardous waste. The following are some ways in which you can properly manage construction waste.
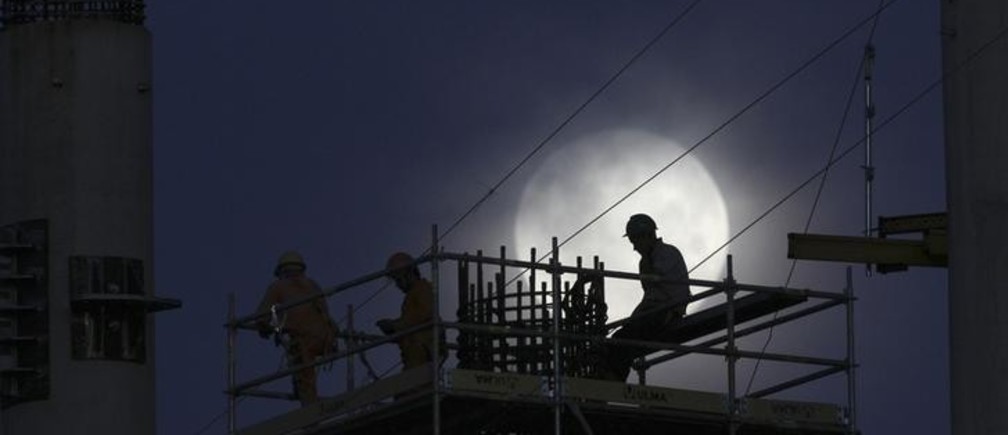
Construction and demolition wastes are typically transported by truck to diversion facilities. The most popular trucks in the United States are medium and light duty trucks. They can be mated together with modular interoperability. It is possible to combine them together. Hazardous waste has four characteristics: corrosivity (ignitability), reactivity and toxicity. The Environment Agency (AE) and California Department of Environmental Quality, (CDEQ), have to manage hazardous waste.
Recyclable
It's important that you take action to reduce the amount construction waste that ends up in the landfills. California Green Building Standards Code requires that builders prepare a plan for managing construction waste before they can be approved and permitted. There are many materials that you can recycle: wood, vegetation, metals, insulation and ceiling tiles. Some composites like Hardplan siding can even be recycled.
Recycling construction waste is a great way to save money. First, it helps save energy and reduce the use of natural resources. Recycling all asphalt and concrete waste produced by US construction projects will result in a savings of approximately one billion gallons per year. Next, by recycling your waste, you will be helping the environment by reducing toxic waste in landfills, and preventing it from entering waterways.
Off-site
The Hong Kong Civil Engineering and Development Department has two off-site CWS facilities, which handled 5.11 million tons of construction waste in February 2012. This program needs to be improved in order to produce better results. This paper will examine the CWS program practices in Hong Kong and provide practical examples of how to improve them. This will allow construction professionals to reduce waste and lower hauling costs. Contractors should tell suppliers to cut down on packaging to ensure a more efficient program for managing waste.
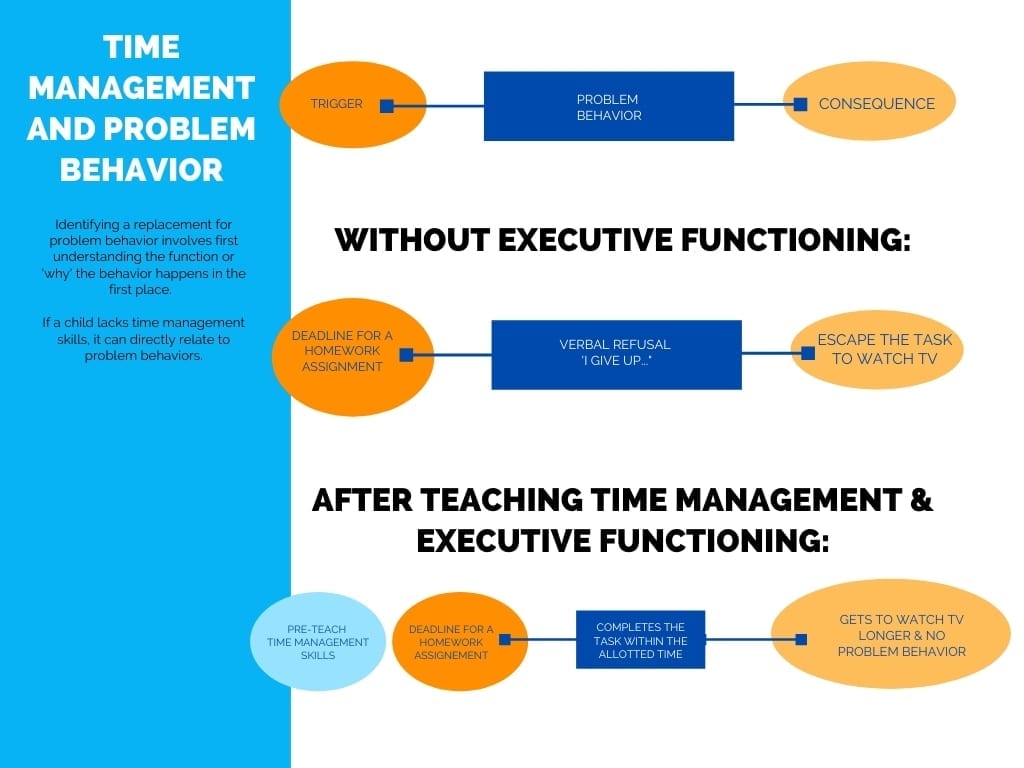
Another advantage of construction waste off-site is the ability to identify the material easily and quickly. For the economic viability and viability of CWS off-site, it is crucial to correctly identify materials. Many contractors, subcontractors, and project specifications include protocols for jobsite waste management. In order to manage construction waste, building owners might also have policies and guidelines in place. Some service providers may even provide containers to store materials. It is vital to be aware of the legal requirements as well as the costs involved in construction waste disposal or recycling.
FAQ
What are the 3 main management styles?
There are three main management styles: participative, laissez-faire and authoritarian. Each style has its strengths and weaknesses. Which style do your prefer? Why?
Autoritarian – The leader sets the direction for everyone and expects them to follow. This style works well if an organization is large and stable.
Laissez-faire is a leader who allows everyone to make their own decisions. This approach works best in small, dynamic organizations.
Participative - The leader listens to ideas and suggestions from everyone. This style is most effective in smaller organizations, where everyone feels valued.
What are the five management methods?
These five stages are: planning, execution monitoring, review and evaluation.
Planning involves setting goals for the future. Planning involves defining your goals and how to get there.
Execution occurs when you actually carry out the plans. It is important to ensure that everyone follows the plans.
Monitoring is the process of evaluating your progress toward achieving your objectives. Regular reviews of performance against targets, budgets, and other goals should be part.
At the end of every year, reviews take place. They allow for an assessment of whether all went well throughout the year. If not there are changes that can be made to improve the performance next year.
Following the annual review, evaluation is done. It helps identify what worked well and what didn't. It also provides feedback on the performance of people.
What is the difference in a project and program?
A project is temporary, while a program lasts forever.
A project typically has a defined goal and deadline.
This is often done by a group of people who report to one another.
A program will usually have a set number of goals and objectives.
It is often implemented by one person.
What is TQM, exactly?
The quality movement was born during the industrial revolution when manufacturing companies realized they could not compete on price alone. They had to improve efficiency and quality if they were to remain competitive.
In response to this need for improvement, management developed Total Quality Management (TQM), which focused on improving all aspects of an organization's performance. It included continuous improvement and employee involvement as well as customer satisfaction.
Statistics
- This field is expected to grow about 7% by 2028, a bit faster than the national average for job growth. (wgu.edu)
- 100% of the courses are offered online, and no campus visits are required — a big time-saver for you. (online.uc.edu)
- The profession is expected to grow 7% by 2028, a bit faster than the national average. (wgu.edu)
- As of 2020, personal bankers or tellers make an average of $32,620 per year, according to the BLS. (wgu.edu)
- Hire the top business lawyers and save up to 60% on legal fees (upcounsel.com)
External Links
How To
What is Lean Manufacturing?
Lean Manufacturing uses structured methods to reduce waste, increase efficiency and reduce waste. They were created in Japan by Toyota Motor Corporation during the 1980s. The aim was to produce better quality products at lower costs. Lean manufacturing is about eliminating redundant steps and activities from the manufacturing process. It is composed of five fundamental elements: continuous improvement; pull systems, continuous improvements, just-in–time, kaizen, continuous change, and 5S. Pull systems involve producing only what the customer wants without any extra work. Continuous improvement refers to continuously improving existing processes. Just-in time refers to components and materials being delivered right at the place they are needed. Kaizen means continuous improvement, which is achieved by implementing small changes continuously. Five-S stands for sort. It is also the acronym for shine, standardize (standardize), and sustain. To achieve the best results, these five elements must be used together.
The Lean Production System
Six key concepts make up the lean manufacturing system.
-
Flow - focus on moving material and information as close to customers as possible;
-
Value stream mapping: This is a way to break down each stage into separate tasks and create a flowchart for the entire process.
-
Five S's - Sort, Set In Order, Shine, Standardize, and Sustain;
-
Kanban: Use visual signals such stickers, colored tape, or any other visual cues, to keep track your inventory.
-
Theory of constraints: Identify bottlenecks and use lean tools such as kanban boards to eliminate them.
-
Just-in-time delivery - Deliver components and materials right to your point of use.
-
Continuous improvement: Make incremental improvements to the process instead of overhauling it completely.