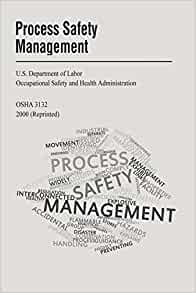
Obtaining engineering project management training is a good way to ensure you'll be prepared to manage projects. Not only will you have the technical skills and knowledge to do these tasks, but you'll also learn how interact with others to get the job done.
You'll also be able to take a look at a variety of different project management methods and tools. Learn how to create a work breakdown structure and estimate costs. You will also learn how to calculate earned and develop a project program, manage issues throughout the project cycle, and deal with any problems.
Project engineers generally have at most three years of experience. They need to be skilled at project management and can make quick decisions so that they can be productive on the job. They must also be able to communicate clearly and write reports that are understandable by non-engineers. They are often required to travel to consult contractors and to work on the job site. They may occasionally also be required to work in the office.
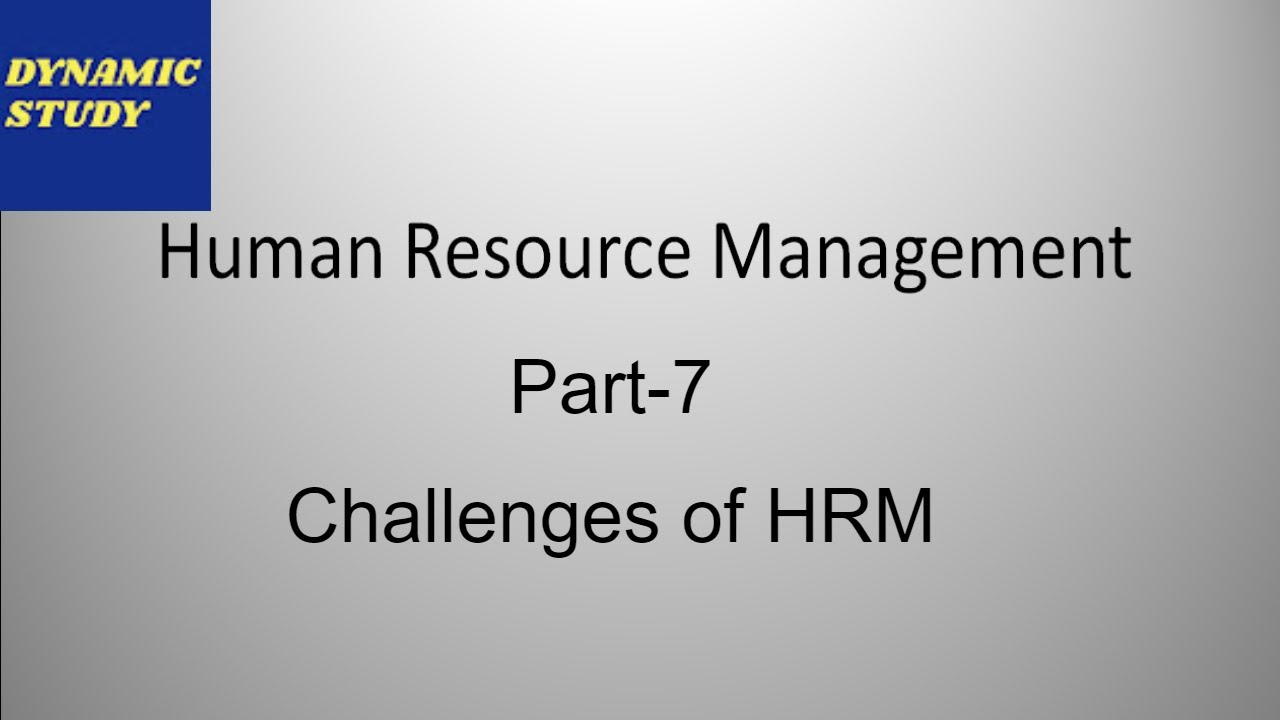
Earning an engineering degree is the best way to become a project engineers. You can also learn the skills and knowledge necessary to succeed in this field through a variety of different methods, including internships and training courses. You will need to be willing to invest the time and effort required to get the best out of your training, regardless of your educational background.
Project engineering training goes far beyond standard scheduling. It includes practical exercises and workshops. You will also get real-world examples to help you apply the knowledge you have learned. The skills you'll learn will be put to use in real-world situations, which will allow you to succeed in engineering.
Design is one of the most fundamental aspects of project engineering. This process will help you better understand your project's requirements and create efficient designs. You'll also learn how CAD drawings can be used to create accurate designs.
You'll also want to study how to write a well-constructed requirements document. It is also important to understand how to make a project plan and include a critical path schedule. Learn how to calculate earned worth and compare cost estimates. You'll also be able to find out the real cost of quality.
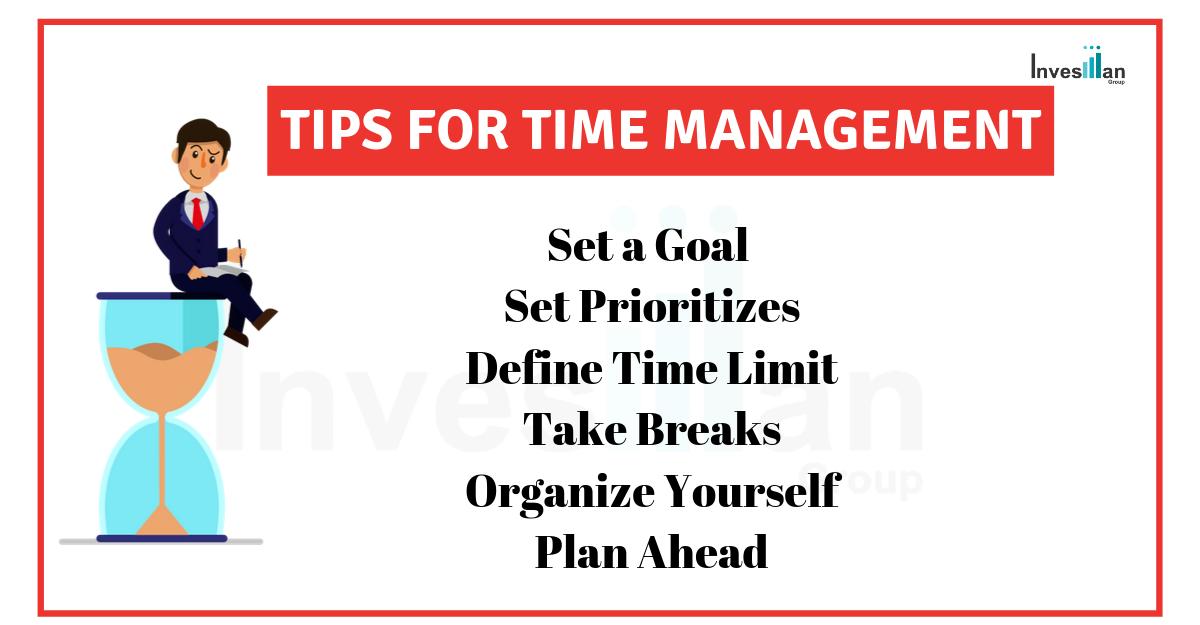
A project engineer needs to be proficient in trigonometry, as well as mathematics. Because complex problems can only be solved with a solid foundation in math, this is a must-have skill. You'll also need to know how to calculate the net present value of a project, which demonstrates how the project will benefit the customer. You'll also want to consider the business case for the project, which involves analyzing the stakeholder needs and expectations, determining the key deliverables and identifying the business case.
The Project Management Institute offers a PMP credential that indicates knowledge and experience in project management. In order to obtain this credential, you'll need to take a test and pass it. Your certification must be maintained for three years.
FAQ
Six Sigma is so popular.
Six Sigma is simple to implement and can yield significant results. It can also be used to help companies identify and focus on the most important aspects of their business.
What are the most important management skills?
Any business owner needs to be able to manage people, finances, resources and time. These include the ability and willingness to manage people, finances as well resources, time and space.
These skills are necessary for setting goals and objectives as well as planning strategies, leading groups, motivating employees and solving problems.
You can see that there are many managerial duties.
What kind people use Six Sigma?
Six sigma is a common concept for people who have worked in statistics or operations research. But anyone can benefit from it.
Because it requires a high level of commitment, only those with strong leadership skills will make an effort necessary to implement it successfully.
Statistics
- The average salary for financial advisors in 2021 is around $60,000 per year, with the top 10% of the profession making more than $111,000 per year. (wgu.edu)
- 100% of the courses are offered online, and no campus visits are required — a big time-saver for you. (online.uc.edu)
- This field is expected to grow about 7% by 2028, a bit faster than the national average for job growth. (wgu.edu)
- Our program is 100% engineered for your success. (online.uc.edu)
- UpCounsel accepts only the top 5 percent of lawyers on its site. (upcounsel.com)
External Links
How To
How do I do the Kaizen Method?
Kaizen means continuous improvement. This Japanese term refers to the Japanese philosophy of continuous improvement that emphasizes incremental improvements and constant improvement. It's a team effort to continuously improve processes.
Kaizen is one of Lean Manufacturing's most efficient methods. In this concept, employees who are responsible for the production line must identify problems that exist during the manufacturing process and try to solve them before they become big issues. This way, the quality of products increases, and the cost decreases.
Kaizen is an approach to making every worker aware and alert to what is happening around them. If something is wrong, it should be corrected immediately so that no problem occurs. If someone spots a problem while at work, they should immediately report it to their manager.
There are some basic principles that we follow when doing kaizen. Start with the end product, and then move to the beginning. To improve our factory, for example, we need to fix the machines that produce the final product. Next, we repair the machines that make components. Then, the machines that make raw materials. Finally, we repair the workers who are directly involved with these machines.
This method is known as kaizen because it focuses upon improving every aspect of the process step by step. We finish fixing the factory and then go back to the beginning. This continues until we achieve perfection.
How to measure kaizen's effectiveness in your business is essential to implement it. There are several ways to determine whether kaizen is working well. One of these ways is to check the number of defects found on the finished products. Another way is to see how much productivity has increased since implementing kaizen.
A good way to determine whether kaizen has been implemented is to ask why. You were trying to save money or obey the law? Did you really believe it would lead to success?
Congratulations! Now you're ready for kaizen.