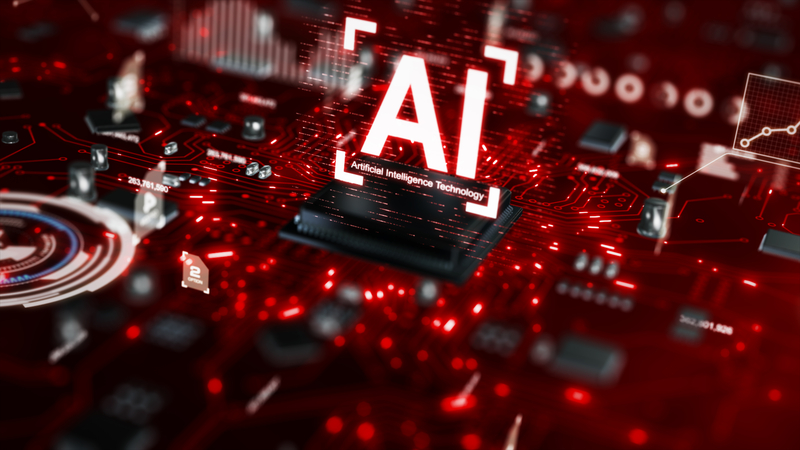
You can learn more about the latest trends and how they will impact your business through supply chain webinars. Many are open to all and free of charge. Learn more about Supply Chain Management, AI and Machine Learning. These events even cover Industry 4.0 technologies, as well multiparty control towers. These events, which are free to attend, are a great way for you to find out more about the latest supply chain technology.
Machine Learning
Machine Learning can be used in many ways throughout your supply chain. For example, it can optimize factory schedules, balance build-to-order and made-to-stock workflows, and prevent material delays during production. Machine learning can also detect fraud. It analyses real-time data to detect anomalies and patterns, and notifies supply chain managers of potential problems.
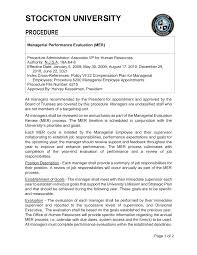
AI
Supply chains can benefit from predictive analytics. Interpreting the data generated with this technology can prove difficult. This webinar will help supply chain executives understand the basics and how AI can be applied to their business.
Industry 4.0 technologies
Industry 4.0 technologies, otherwise known as the digital supply chain, are a major shift in the way businesses conduct business. The speed of change makes it challenging to distill the competitive advantage from the new technologies. This Capstone Webinar will discuss the key domains of change and the agents behind the transformation. The webinar will also address some of the most common questions about key technologies.
Multiparty control towers
Multiparty control rooms are an important component of the supply chain and offer many benefits for companies. They enable companies to automate repetitive tasks and save money and time. When combined with orchestration platforms, multiparty command towers can be powerful tools. These solutions can link all parts of the supply chain ecosystem. They provide a single source to truth for all those involved.
Collaboration within the supply chain
Collaboration within the supply network is becoming an increasingly popular strategy. It can deliver significant benefits to companies' bottom lines. Collaboration is a great way to increase operational efficiency and foster innovation. There are some important aspects to remember when collaborating across horizontal and vertical dimensions.
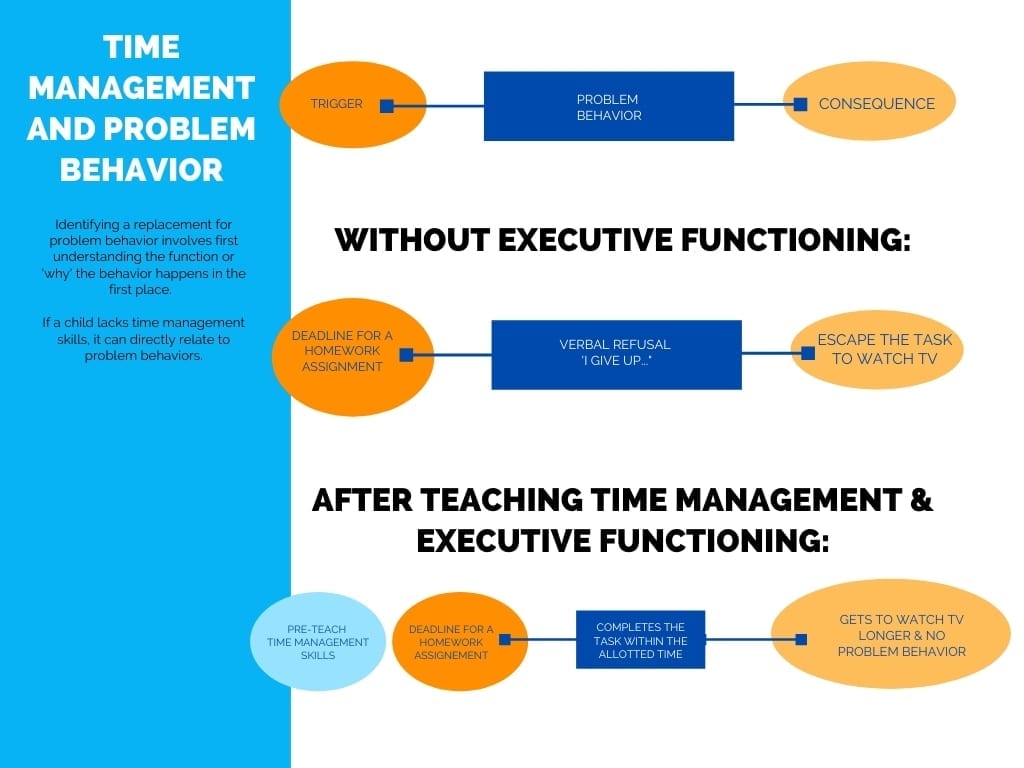
The future of the supply chain
Future of the supply-chain webinars will address the problems that are affecting supply chains. They address how to make them sustainable and integrate corporate governance into the value chains. They will also discuss the ways in which to manage increasing antitrust and ESG convergence. The session will focus on trends in supply chains starting in 2022, and continuing into the future.
FAQ
What's the difference between leadership & management?
Leadership is about being a leader. Management is all about controlling others.
Leaders inspire followers, while managers direct workers.
A leader motivates people and keeps them on task.
A leader develops people; a manager manages people.
What are the 3 basic management styles?
These are the three most common management styles: participative (authoritarian), laissez-faire (leavez-faire), and authoritarian. Each style is unique and has its strengths as well as weaknesses. Which style do YOU prefer? Why?
Authoritarian - The leader sets the direction and expects everyone to comply with it. This style works well if an organization is large and stable.
Laissez-faire – The leader gives each individual the freedom to make decisions for themselves. This style is best when the organization has a small but dynamic group.
Participative: The leader listens to everyone's ideas and suggestions. This approach works best in small organizations where everyone feels valued.
Why does it sometimes seem so difficult to make good business decisions?
Complex systems are often complex and have many moving parts. The people who run them must juggle multiple priorities at once while also dealing with uncertainty and complexity.
The key to making good decisions is to understand how these factors affect the system as a whole.
It is important to consider the functions and reasons for each part of the system. It's important to also consider how they interact with each other.
You need to ask yourself if your previous actions have led you to make unfounded assumptions. If so, it might be worth reexamining them.
You can always ask someone for help if you still have questions after all of this. You might find their perspective is different from yours and they may have insight that can help you find the solution.
What is Six Sigma?
Six Sigma uses statistical analysis to find problems, measure them, analyze root causes, correct problems, and learn from experience.
The first step to solving the problem is to identify it.
Next, data will be collected and analyzed to determine trends and patterns.
Then corrective actions are taken to solve the problem.
Finally, data will be reanalyzed to determine if there is an issue.
This cycle continues until there is a solution.
What is the difference between Six Sigma Six Sigma and TQM?
The main difference in these two quality management tools lies in the fact that six sigma is focused on eliminating defects and total quality management (TQM), emphasizes improving processes and reducing costs.
Six Sigma is a method for continuous improvement. This method emphasizes eliminating defects using statistical methods such p-charts, control charts, and Pareto analysis.
This method has the goal to reduce variation of product output. This is accomplished through identifying and correcting root causes.
Total quality management is the measurement and monitoring of all aspects within an organization. Training employees is also part of total quality management.
It is frequently used as an approach to increasing productivity.
Why is it important that companies use project management methods?
Project management techniques are used to ensure that projects run smoothly and meet deadlines.
This is because most businesses rely on project work for their products and services.
These projects require companies to be efficient and effective managers.
Companies that do not manage their projects effectively risk losing time, money, or reputation.
What is TQM?
The quality movement was born during the industrial revolution when manufacturing companies realized they could not compete on price alone. They had to improve efficiency and quality if they were to remain competitive.
To address this need for improvement management created Total Quality Management (TQM) which aimed to improve all aspects of an organization's performance. It included continuous improvement processes, employee involvement, and customer satisfaction.
Statistics
- The BLS says that financial services jobs like banking are expected to grow 4% by 2030, about as fast as the national average. (wgu.edu)
- The average salary for financial advisors in 2021 is around $60,000 per year, with the top 10% of the profession making more than $111,000 per year. (wgu.edu)
- Hire the top business lawyers and save up to 60% on legal fees (upcounsel.com)
- The profession is expected to grow 7% by 2028, a bit faster than the national average. (wgu.edu)
- As of 2020, personal bankers or tellers make an average of $32,620 per year, according to the BLS. (wgu.edu)
External Links
How To
How do you implement a Quality Management Plan (QMP)?
QMP, which was introduced by ISO 9001:2008, is a systematic approach to improving products, services, and processes through continuous improvement. It emphasizes on how to continuously measure, analyze, control, and improve processes, product/service, and customer satisfaction.
QMP stands for Quality Management Process. It is used to guarantee good business performance. The QMP aims to improve the process of production, service delivery, and customer relationship. QMPs should cover all three dimensions - Products, Processes, and Services. When the QMP includes only one aspect, it is called a "Process" QMP. When the QMP focuses on a Product/Service, it is known as a "Product" QMP. The QMP that focuses on customer relationships is known as the "Customer" QMP.
Scope, Strategy and the Implementation of a QMP are the two major elements. These are the following:
Scope: This describes the scope and duration for the QMP. For example, if your organization wants to implement a QMP for six months, this scope will define the activities performed during the first six months.
Strategy: These are the steps taken in order to reach the goals listed in the scope.
A typical QMP has five phases: Planning (Design, Development), Implementation (Implementation), and Maintenance. Each phase is explained below:
Planning: In this stage, the objectives of the QMP are identified and prioritized. All stakeholders involved in the project are consulted to understand their requirements and expectations. Once the objectives and priorities have been identified, it is time to plan the strategy to achieve them.
Design: The design stage involves the development of vision, mission strategies, tactics, and strategies that will allow for successful implementation. These strategies are executed by creating detailed plans.
Development: The development team is responsible for building the resources and capabilities necessary to implement the QMP effectively.
Implementation: This involves the actual implementation of the QMP using the planned strategies.
Maintenance: This is an ongoing procedure to keep the QMP in good condition over time.
In addition, several additional items must be included in the QMP:
Participation of Stakeholders: The QMP's success depends on the participation of stakeholders. They should actively be involved during the planning and development, implementation, maintenance, and design stages of QMP.
Project Initiation: It is essential to have a clear understanding about the problem and the solution before you can initiate a project. Also, the initiator should understand why they are doing it and what they expect.
Time frame: It is crucial to know the time frame for the QMP. A simple version is fine if you only plan to use the QMP for a brief period. If you are looking for a longer-term commitment, however, you might need more complex versions.
Cost Estimation is another important aspect of the QMP. Without knowing how much you will spend, planning is impossible. The QMP should be cost-estimated before it can begin.
QMPs are more than just documents. They can also be updated as needed. It changes as the company grows. It should therefore be reviewed frequently to ensure that the organization's needs are met.