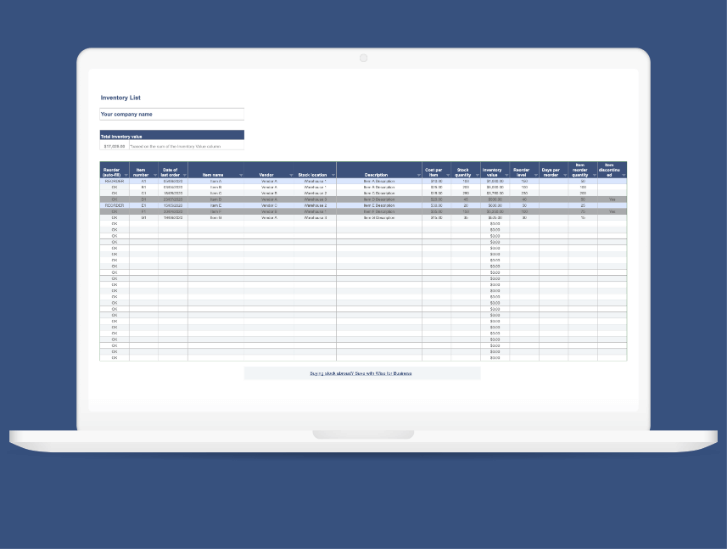
You should think about several things when thinking about a career in supply-chain management. There are many different types of supply chains, and different industries have different supply chains. If you are interested in working as a wholesaler or retailer, then a supply chain manager for a manufacturing firm is not the best choice.
The characteristics of a successful supply-chain manager
Successful supply chain managers are versatile learners who have an open mind to experimentation and change. They quickly understand the complexities of a problem and can use failures as learning opportunities. They love the challenge of undertaking new tasks and are quick to grasp the essence of anything. Their natural curiosity fuels their drive to learn new things.
While supply chain managers cannot become micromanagers they must excel at strategic risk-taking. Risks are a natural part of growth, but they must be backed by data. This means being strategic and analytical rather than reactive. Inflexibility hinders success. It can also frustrate supply chain managers.
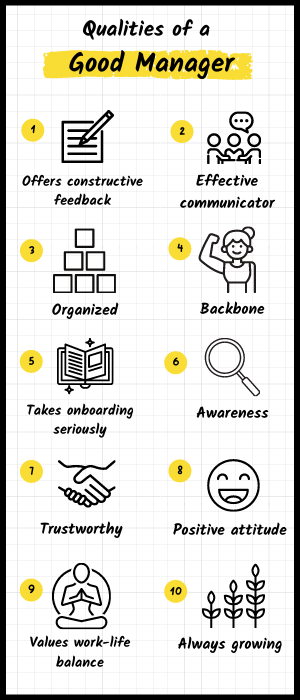
Management of a supply network is complex and changing. Supply chain managers need to be aware of market trends and proactive in implementing new technology. They also must be able to effectively communicate with people with advanced technological knowledge.
A bachelor's degree is required in supply chain management.
A bachelor's degree in supply chain management gives students a foundation in business administration, strategic management, and leadership. This degree also builds upon the skills necessary for common software applications. A degree in supply-chain management that is accredited can be obtained for a relatively affordable price. For a full-time degree in supply chain management, the average cost for an undergraduate degree at a public four-year university was $10,560 annually. Private universities charge $37,650. Financial aid can reduce this amount and federal student loans can help you finance your degree.
An accredited university may offer an online degree in supply-chain management. This can be a great option. This program covers topics such as international supply chains, global supply chain management, and business decision making. Additional coursework includes operational strategies and sustainability in global supplies chains. The program costs approximately $688 per credit-hour.
Typical job duties of a supply chain manager
Managers of the supply chain are responsible to organize a company’s supply network. They plan the flow for products, manage inventory, and set up processes to cut costs. They also manage third-party logistics companies, identify waste, perform environmental performance assessments, and handle other administrative tasks. These professionals create monthly, weekly and daily reports that reflect their performance metrics.
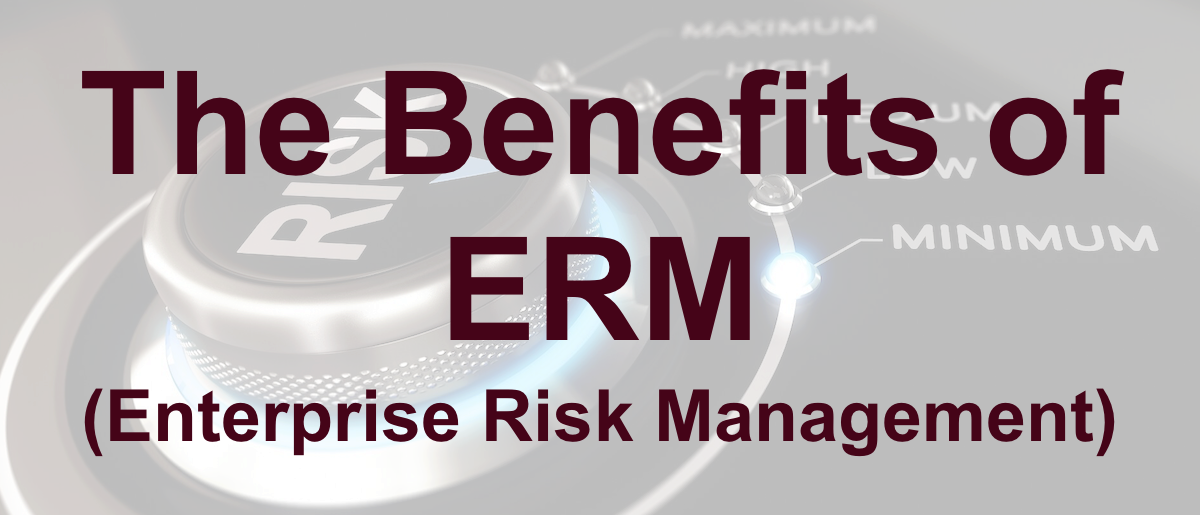
Most supply chain managers work forty hours per semaine and are often located in business settings, sometimes far from the manufacturing floor. The role requires extensive knowledge of the business, operations, and processes within the organization. They should be comfortable working with data and people. A career as a supply-chain manager is a great choice if you like following processes and working with ideas.
The salary for a supply chain manager may be slightly less than the one of a director or procurement. However, the two roles require similar skills, knowledge and abilities in logistics, procedures, as well as customer service.
FAQ
How can a manager motivate his/her staff?
Motivation is the desire for success.
Enjoyable activities can motivate you.
You can also feel motivated by making a positive contribution to the success in the organization.
If you are a doctor and want to be one, it will likely be more rewarding to see patients than to read medical books every day.
The inner motivation is another type.
Perhaps you have a strong sense to give back, for example.
Maybe you like working hard.
If you don't feel motivated, ask yourself why.
Then think about how you can make your life more motivating.
How does a manager learn to manage?
Good management skills are essential for success.
Managers must continuously monitor the performance levels of their subordinates.
You must act quickly if you notice that your subordinate isn’t performing to their standards.
It is important to be able identify areas that need improvement and what can be done to improve them.
What are the top management skills?
Managerial skills are crucial for every business owner, regardless of whether they run a small store in their locality or a large corporation. They are the ability to manage people and finances, space, money, and other factors.
You will need management skills to set goals and objectives, plan strategies, motivate employees, resolve problems, create policies and procedures, and manage change.
As you can see, there are many managerial responsibilities!
Statistics
- Your choice in Step 5 may very likely be the same or similar to the alternative you placed at the top of your list at the end of Step 4. (umassd.edu)
- UpCounsel accepts only the top 5 percent of lawyers on its site. (upcounsel.com)
- This field is expected to grow about 7% by 2028, a bit faster than the national average for job growth. (wgu.edu)
- The profession is expected to grow 7% by 2028, a bit faster than the national average. (wgu.edu)
- Hire the top business lawyers and save up to 60% on legal fees (upcounsel.com)
External Links
How To
How can you implement the Kaizen technique?
Kaizen means continuous improvement. The term was coined in the 1950s at Toyota Motor Corporation and refers to the Japanese philosophy emphasizing constant improvement through small incremental changes. It's a process where people work together to improve their processes continuously.
Kaizen is one method that Lean Manufacturing uses to its greatest advantage. In this concept, employees who are responsible for the production line must identify problems that exist during the manufacturing process and try to solve them before they become big issues. This improves the quality of products, while reducing the cost.
Kaizen is a way to raise awareness about what's happening around you. So that there is no problem, you should immediately correct it if something goes wrong. If someone is aware of a problem at work, he/she should inform his/her manager immediately.
Kaizen is based on a few principles. Always start with the end product in mind and work our way back to the beginning. For example, if we want to improve our factory, we first fix the machines that produce the final product. We then fix the machines producing components, and the machines producing raw materials. Then we fix the workers, who directly work with these machines.
This method is known as kaizen because it focuses upon improving every aspect of the process step by step. After we're done with the factory, it's time to go back and fix the problem.
You need to know how to measure the effectiveness of kaizen within your business. There are many ways you can determine if kaizen has been implemented well. One method is to inspect the finished products for defects. Another way is determining how much productivity increased after implementing kaizen.
To determine if kaizen is effective, you should ask yourself why you chose to implement kaizen. You were trying to save money or obey the law? It was a way to save money or help you succeed.
If you answered yes to any one of these questions, congratulations! You are ready to start kaizen.