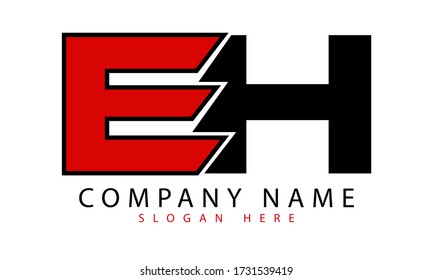
Resourcing is the process of identifying and completing tasks. This includes both the human and the material resources. This can be achieved by purchasing or hiring workers. Once resources are purchased, they should be allocated to different tasks. Project managers can turn to resource managers for help in allocating resources in order ensure that projects run on time and within budget.
Allocation of resources
Resource allocation is an important aspect of project management. There are many things to consider such as the project's timeline, budget, and available resource. The key to efficient resource allocation is a clear scope of the project. A well-defined scope ensures that resources are allocated based on need and priority. A precise scope is also helpful in setting deadlines and budget.
A well-planned resource allocation plan will make it easier to plan the project from start through completion. It will assist in identifying details early on, which will prevent the need to re-allocate resources later. This method works best when the project has a predictable beginning and ending. Plan will contain high-priority tasks which must be completed within the given time frame.
Resources for cost
Cost resources are placeholders to represent the costs of a certain type. They can be used on multiple tasks. For example, two tasks that require plane trips will each require a different airfare resource. A cost resource is entered in the task information dialog box when it is assigned. This allows you to see the true cost.
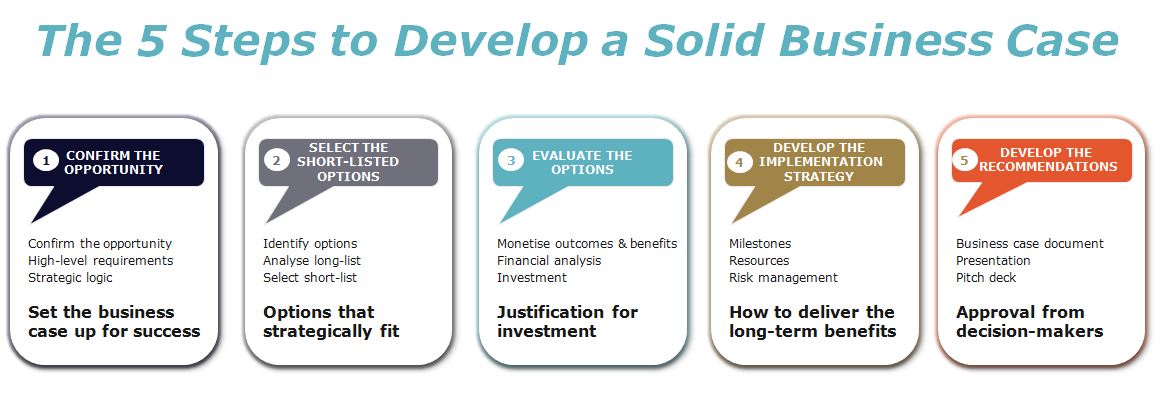
Fixed costs can be variable or fixed costs. This allows you to control the cost of a task by using the variable costs. Cost resources can be associated with tasks such as travel and client meetings. These costs can be protected by project accounting, but their currency does not depend on the actual work performed. This means that as tasks are changed, cost resources may change.
Stakeholder management
In a typical project, there are two parts: the project team and the stakeholders. The stakeholders will have an impact on the success of the project. Members of the project team will be involved in creating the project. The ResMP document documents the roles, responsibilities and responsibilities of each member of the team. The stakeholder list is the document that lists all the stakeholders required for the project.
Stakeholders must be identified early in the project and their interests and influence should be assessed. The relationships between the project team, stakeholders, and their staff must be positive and productive. During the stakeholder identification phase, the project manager should identify potential stakeholders, their roles and departments, and their interests, knowledge, and influence. The level of influence that stakeholders have can lead to them being divided into groups based on authority, legitimacy or concerns.
Automation
Modern project managers can use automation to improve their resourcing management. This automation allows teams focus on high-value and cognitively engaging work which results in higher ROI. Over the past decade, software-as-a-service tools have proliferated, making companies more efficient than ever before. The sheer volume of these tools can impact employee productivity.
Automation of work involves applying technologies, programs, and robotics to achieve specific outcomes with minimal or no human input. It is not intended to replace project managers but to free them from administrative tasks and let them focus on more valuable activities. You can see the benefits of automation in every aspect of a project: from the creation or management of existing products or services, to the management and development of new ones.
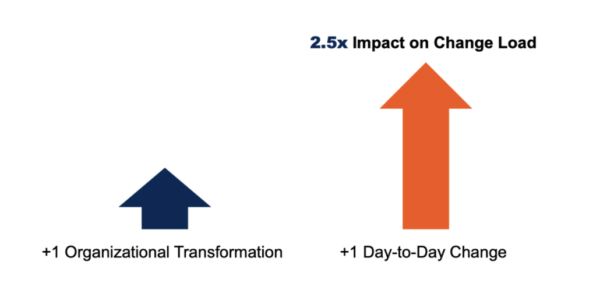
Templates
Resource management is an integral part of any project. Project managers can use templates to help plan for their resources and teams. These templates can be downloaded for free and don't require special software. They are compatible with spreadsheet tools. They enable project managers to adjust the durations and time periods for different projects. This allows each resource to work on multiple projects simultaneously.
There are many free templates available online. They can be customized to meet the specific needs of a project team, and they help to visualize how tasks connect to each other. They can also be used to compare the project's progress with the original schedule. Some templates are more complex than others, and others are designed for specific tasks or phases of the project.
FAQ
What is the difference between TQM and Six Sigma?
The main difference in these two quality management tools lies in the fact that six sigma is focused on eliminating defects and total quality management (TQM), emphasizes improving processes and reducing costs.
Six Sigma is an approach for continuous improvement. This method emphasizes eliminating defects using statistical methods such p-charts, control charts, and Pareto analysis.
This method attempts to reduce variations in product output. This is achieved by identifying and addressing the root causes of problems.
Total Quality Management involves monitoring and measuring every aspect of the organization. It also includes training employees to improve performance.
It is often used as a strategy to increase productivity.
What is Six Sigma?
It is a way to improve quality that places emphasis on customer service and continuous learning. The objective is to eliminate all defects through statistical methods.
Motorola's 1986 efforts to improve manufacturing process efficiency led to the creation of Six Sigma.
This idea quickly spread throughout the industry. Today, many organizations use six sigma methods for product design, production and delivery.
What is a basic management tool used in decision-making?
The decision matrix is a powerful tool that managers can use to help them make decisions. They can think about all options and make informed decisions.
A decision matrix represents alternatives in rows and columns. This allows one to see how each alternative impacts other options.
In this example, we have four possible alternatives represented by the boxes on the left side of the matrix. Each box represents an alternative. The top row shows the status quo (the current situation), and the bottom row shows what would happen if nothing was done at all.
The middle column shows the effect of choosing Option 1. It would translate into an increase in sales from $2million to $3million.
The following columns illustrate the impact of Options 2 and 3. These are positive changes - they increase sales by $1 million and $500 thousand respectively. But, they also have some negative consequences. Option 2 increases the cost of goods by $100,000. Option 3 decreases profits and makes them less attractive by $200,000.
The final column shows results of choosing Option 4. This will result in sales falling by $1,000,000
The best thing about using a decision matrix is that you don't need to remember which numbers go where. It's easy to see the cells and instantly know if any one of them is better than another.
The matrix has already done all of the work. It's as easy as comparing numbers in the appropriate cells.
Here's a sample of how you might use decision matrixes in your business.
You want to decide whether or not to invest more money into advertising. This will allow you to increase your revenue by $5000 per month. However, additional expenses of $10 000 per month will be incurred.
You can calculate the net result of investing in advertising by looking at the cell directly below the one that says "Advertising." That number is $15 thousand. Advertising is a worthwhile investment because it has a higher return than the costs.
What are the steps to take in order to make a management decision?
The decision-making process of managers is complicated and multifaceted. It involves many elements, including analysis, strategy. planning. implementation. measurement. evaluation. feedback.
It is important to remember that people are human beings, just like you. They make mistakes. As such, there are always opportunities for improvement, especially when you put in the effort to improve yourself.
This video shows you how management makes decisions. We discuss the different types of decisions and why they are important, every manager should know how to navigate them. These topics are covered in this course:
What is the difference between management and leadership?
Leadership is about inspiring others. Management is about controlling others.
Leaders inspire others, managers direct them.
Leaders inspire people to achieve success. Managers keep their workers focused.
A leader develops people; a manager manages people.
What is the difference in a project and program?
A program is permanent, whereas a project is temporary.
A project usually has a specific goal and deadline.
It is often performed by a team of people, who report back on someone else.
A program typically has a set goal and objective.
It is usually implemented by a single person.
How does Six Sigma work
Six Sigma uses statistical analyses to locate problems, measure them, analyze root cause, fix problems and learn from the experience.
The first step is identifying the problem.
The next step is to collect data and analyze it in order to identify trends or patterns.
The problem is then rectified.
The data are then reanalyzed to see if the problem is solved.
This cycle continues until there is a solution.
Statistics
- Your choice in Step 5 may very likely be the same or similar to the alternative you placed at the top of your list at the end of Step 4. (umassd.edu)
- As of 2020, personal bankers or tellers make an average of $32,620 per year, according to the BLS. (wgu.edu)
- Our program is 100% engineered for your success. (online.uc.edu)
- The average salary for financial advisors in 2021 is around $60,000 per year, with the top 10% of the profession making more than $111,000 per year. (wgu.edu)
- 100% of the courses are offered online, and no campus visits are required — a big time-saver for you. (online.uc.edu)
External Links
How To
How can you use the Kaizen method?
Kaizen means continuous improvement. Kaizen is a Japanese concept that encourages constant improvement by small incremental changes. This is a collaborative process in which people work together to improve their processes continually.
Kaizen is one method that Lean Manufacturing uses to its greatest advantage. Kaizen is a concept where employees in charge of the production line are required to spot problems during the manufacturing process before they become major issues. This improves the quality of products, while reducing the cost.
Kaizen is about making everyone aware of the world around them. If something is wrong, it should be corrected immediately so that no problem occurs. If someone spots a problem while at work, they should immediately report it to their manager.
When doing kaizen, there are some principles we must follow. We always start from the end product and move toward the beginning. For example, if we want to improve our factory, we first fix the machines that produce the final product. Next, we fix the machines which produce components. Finally, we repair the workers who are directly involved with these machines.
This method is known as kaizen because it focuses upon improving every aspect of the process step by step. We finish fixing the factory and then go back to the beginning. This continues until we achieve perfection.
You need to know how to measure the effectiveness of kaizen within your business. There are many ways to tell if kaizen is effective. One of these ways is to check the number of defects found on the finished products. Another way is to check how much productivity has grown since kaizen was implemented.
A good way to determine whether kaizen has been implemented is to ask why. It was because of the law, or simply because you wanted to save some money. You really believed it would make you successful?
If you answered yes to any one of these questions, congratulations! You're ready to start kaizen.