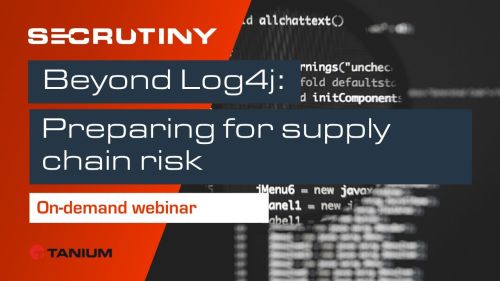
The Waste Management specialist is responsible for the development of project schedules as well as making service recommendations. This position works in partnership with the National Account Manager to develop client relationships and create new programs. As a member of the team, the Waste Management Specialist recruits associates to achieve professional standards and actively participates in professional development. To ensure clients receive the best service, they work closely with the National Account Manager. This position oversees projects, and also leads project teams.
Jim Bentley
Advanced Disposal National Accounts (also known as the commercial division) is a waste management company. Jim Bentley will be responsible to develop relationships with clients and prospective clients as well as strategic vendor partners. He will also manage business development with other companies within the company's vast network of over 7,000 environmental service providers throughout North America. Bentley has more than 21 years experience in solid waste management, most recently working as a senior executive for Green Leaf Compaction.
Ashish Sharma
Senior manager of digital for Waste Management, Ashish Sharma leads digital solutions and technology teams in the company's Asset Management business unit. He also manages the digital team responsible for New York's Marine Transfer Station Project. He joined Waste Management as a senior leader in 2014. He previously held senior leadership roles at IBM and Deloitte & Touche, LLC. He has more that 16 years of industry experience.
Sharma has been involved in many projects while at Waste Management. He was recently involved in the construction of New York's marine transfer station. This facility supported Waste Management's $3.3 million contract with the Department of Sanitation. Sharma was also awarded the Waste360 40 Under 40 Award. This recognition highlights his leadership skills and innovation in waste management. Ashish Sharma was awarded numerous industry awards, including "Best Product" from Waste360.
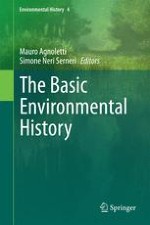
FAQ
What are the five management process?
Each business has five stages: planning, execution and monitoring.
Planning means setting goals for the long-term. It includes defining what you want to achieve and how you plan to do it.
Execution is the actual execution of the plans. It is important to ensure that everyone follows the plans.
Monitoring is a way to track progress towards your objectives. Monitoring should include regular reviews of performance against goals and budgets.
Every year, there are reviews. They provide an opportunity to assess whether everything went well during the year. If not, changes may be made to improve the performance next time around.
After the annual review is complete, evaluations are conducted. It helps to identify what went well and what didn’t. It also provides feedback on the performance of people.
What is TQM and how can it help you?
The industrial revolution saw the realization that prices alone were not sufficient to sustain manufacturing companies. This led to the birth of quality. They needed to improve the quality and efficiency of their products if they were to be competitive.
In response to this need for improvement, management developed Total Quality Management (TQM), which focused on improving all aspects of an organization's performance. It included continual improvement processes, employee involvement, customer satisfaction, and customer satisfaction.
Six Sigma is so popular.
Six Sigma is easy to use and can lead to significant improvements. Six Sigma provides a framework to measure improvements and allows companies to focus on the most important things.
What kind of people use Six Sigma?
Six Sigma is well-known to those who have worked in operations research and statistics. However, anyone involved in any aspect of business can benefit from using it.
It requires high levels of commitment and leadership skills to be successful.
Why is it so hard to make smart business decisions?
Complex systems and many moving parts make up businesses. The people who run them must juggle multiple priorities at once while also dealing with uncertainty and complexity.
Understanding how these factors impact the whole system is key to making informed decisions.
This requires you to think about the purpose and function of each component. It is important to then consider how the individual pieces relate to each other.
You need to ask yourself if your previous actions have led you to make unfounded assumptions. You might consider revisiting them if they are not.
Asking for assistance from someone else is a good idea if you are still having trouble. They might have different perspectives than you, and could offer insight that could help you solve your problem.
Statistics
- The average salary for financial advisors in 2021 is around $60,000 per year, with the top 10% of the profession making more than $111,000 per year. (wgu.edu)
- Your choice in Step 5 may very likely be the same or similar to the alternative you placed at the top of your list at the end of Step 4. (umassd.edu)
- The BLS says that financial services jobs like banking are expected to grow 4% by 2030, about as fast as the national average. (wgu.edu)
- This field is expected to grow about 7% by 2028, a bit faster than the national average for job growth. (wgu.edu)
- As of 2020, personal bankers or tellers make an average of $32,620 per year, according to the BLS. (wgu.edu)
External Links
How To
What is Lean Manufacturing?
Lean Manufacturing techniques are used to reduce waste while increasing efficiency by using structured methods. They were developed in Japan by Toyota Motor Corporation (in the 1980s). The aim was to produce better quality products at lower costs. Lean manufacturing eliminates unnecessary steps and activities from a production process. It includes five main elements: pull systems (continuous improvement), continuous improvement (just-in-time), kaizen (5S), and continuous change (continuous changes). Pull systems involve producing only what the customer wants without any extra work. Continuous improvement refers to continuously improving existing processes. Just-in-time is when components and other materials are delivered at their destination in a timely manner. Kaizen means continuous improvement, which is achieved by implementing small changes continuously. Last but not least, 5S is for sort. To achieve the best results, these five elements must be used together.
Lean Production System
Six key concepts are the basis of lean production:
-
Flow: The goal is to move material and information as close as possible from customers.
-
Value stream mapping - Break down each stage in a process into distinct tasks and create an overview of the whole process.
-
Five S’s - Sorted, In Order. Shine. Standardize. And Sustain.
-
Kanban: Use visual signals such stickers, colored tape, or any other visual cues, to keep track your inventory.
-
Theory of constraints - identify bottlenecks during the process and eliminate them with lean tools like Kanban boards.
-
Just-in-time delivery - Deliver components and materials right to your point of use.
-
Continuous improvement is making incremental improvements to your process, rather than trying to overhaul it all at once.