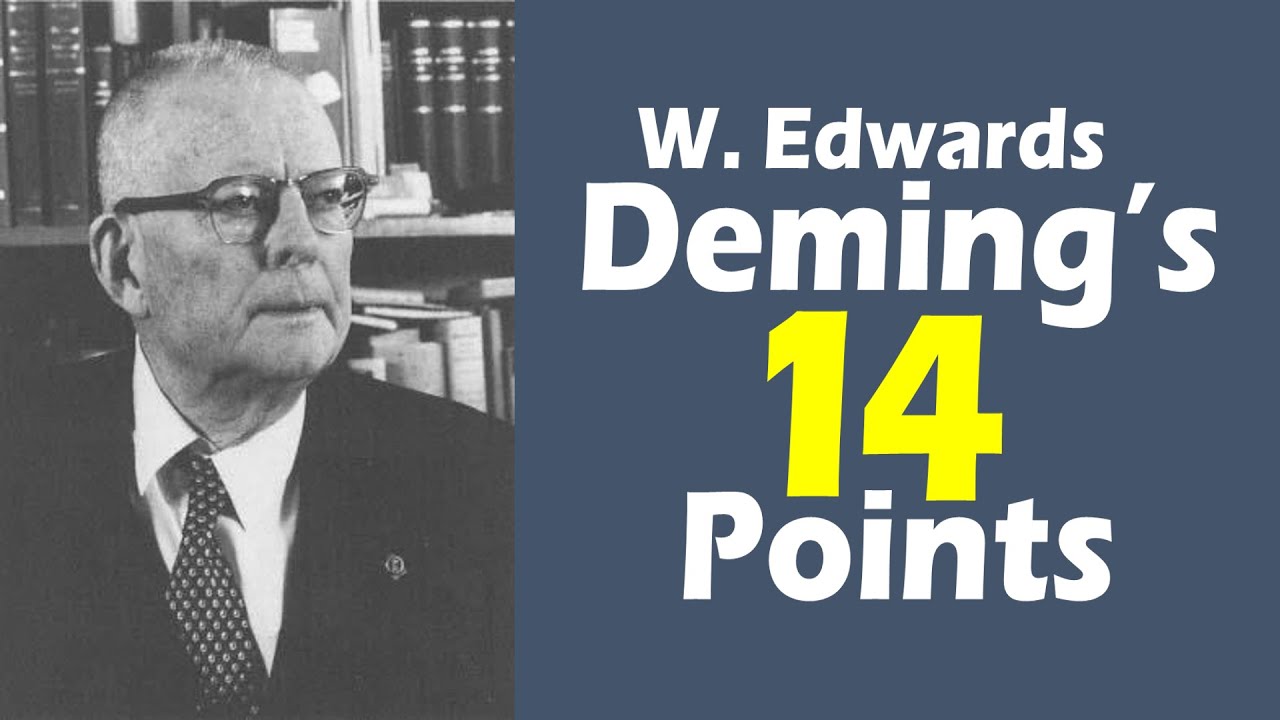
Process safety management aims to ensure that operating systems and processes are safe. This system is a legal requirement for major hazard facilities and must be updated at least every five years. Process safety management is designed to prevent accidents. Here are some steps to help you get started with process safety management. These steps will ensure that your facilities are as safe as possible and help prevent accidents.
Process safety management is a structured framework to manage the integrity of operating systems.
The goal of process safety management (PSM) is to minimize the likelihood of incidents and improve productivity. It is about controlling the risks in the plant and making equipment safer. It requires strict adherence and assessment of hazards. It includes training and maintenance, along with process control. It is an integral part of any safety-conscious organization.
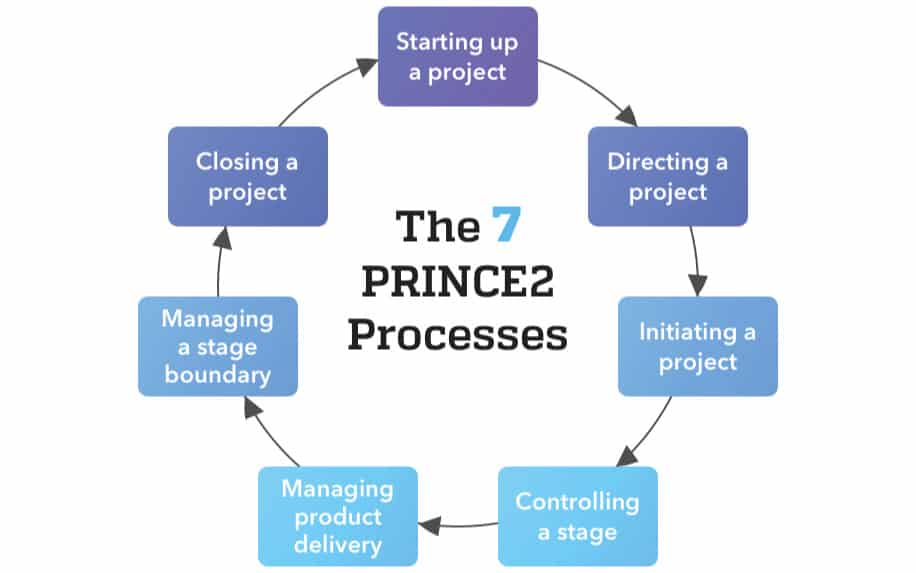
It should be up-to-date every five years
OSHA requires that all processes are reviewed and kept current. This includes the creation of written procedures and safety information. All employees who are involved in the project must have this information. Written investigation reports and procedures must be retained for 5 years. Employees should have easy access to up-to-date process safety information. Employers can seek the assistance of safety risk management consultants to meet their requirements.
It is a legal requirement in order to operate major hazard facilities
The legal requirement to implement a process safety control system for all major hazards is the process safety management program. In addition to developing and implementing the program, employers must implement a procedure for a prompt and safe evacuation of employees. In most cases, this plan includes a safety alarm that will alert employees to evacuate. It should also include emergency procedures that can be used to help employees who are unable physically to evacuate hazardous areas.
It helps to prevent incidents
A well-designed process management system for safety can enhance a company's safety performance and profitability. It can also increase the company's environmental responsibility. In addition, it helps reduce the risk of incidents. These are all vital areas to ensure the company's long-term success. Here's a summary of the benefits of a process management system. It is a system that helps companies prevent and reduce accidents, as well as improve the safety and health of employees and customers.
It takes time.
Process safety management can be complicated and time-consuming in a hazardous chemical plant. OSHA does not regulate process safety management programs. However, OSHA requires facilities to create a plan and meet 14 minimum requirements. For data collection and compilation of risk assessments, and other information, spreadsheets and forms are used by some companies. This can be time-consuming and exposes you to human error.
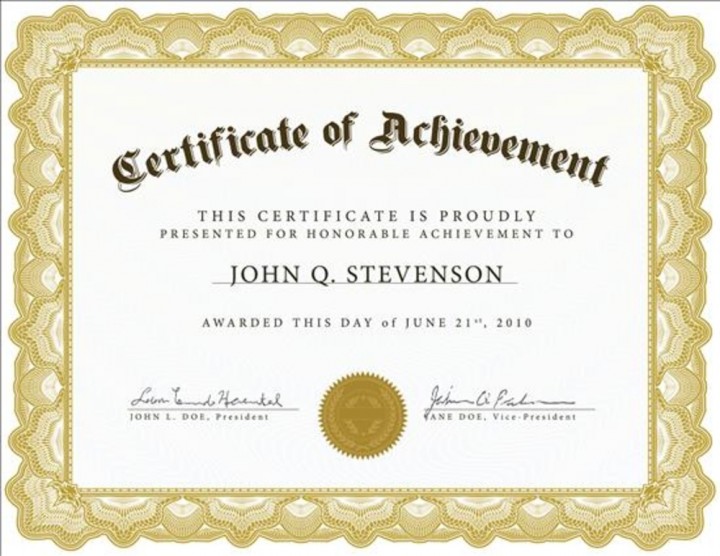
Participation is required from employees
Pennsylvania State University adopted an employee participation element to its PSM program. This element uses employees' unique perspectives, knowledge, and experience to improve safety. The program describes different mechanisms for employee participation and identifies minimum requirements for participation. It is important to include all employees in the process safety management process and involve them in all aspects. Participation by employees in PSM is crucial for avoiding serious accidents. How can you make sure that everyone is involved in the program?
FAQ
What is the difference between project and program?
A program is permanent, whereas a project is temporary.
A project is usually defined by a clear goal and a set deadline.
It is often carried out by a team of people who report back to someone else.
A program often has a set goals and objectives.
It is typically done by one person.
What is the difference in leadership and management?
Leadership is all about influencing others. Management is about controlling others.
Leaders inspire others, managers direct them.
Leaders motivate people to succeed; managers keep workers on track.
A leader develops people; a manager manages people.
What kind of people use Six Sigma
Six Sigma will most likely be familiar to people who have worked in statistics and operations research. But anyone can benefit from it.
Because it requires a high degree of commitment, only leaders with strong leadership skills can implement it successfully.
Six Sigma is so well-known.
Six Sigma is easy and can deliver significant results. It provides a framework that allows for improvement and helps companies concentrate on what really matters.
Statistics
- The BLS says that financial services jobs like banking are expected to grow 4% by 2030, about as fast as the national average. (wgu.edu)
- Your choice in Step 5 may very likely be the same or similar to the alternative you placed at the top of your list at the end of Step 4. (umassd.edu)
- The profession is expected to grow 7% by 2028, a bit faster than the national average. (wgu.edu)
- The average salary for financial advisors in 2021 is around $60,000 per year, with the top 10% of the profession making more than $111,000 per year. (wgu.edu)
- Our program is 100% engineered for your success. (online.uc.edu)
External Links
How To
How does Lean Manufacturing work?
Lean Manufacturing techniques are used to reduce waste while increasing efficiency by using structured methods. They were created in Japan by Toyota Motor Corporation during the 1980s. The main goal was to produce products at lower costs while maintaining quality. Lean manufacturing emphasizes removing unnecessary steps from the production process. It is composed of five fundamental elements: continuous improvement; pull systems, continuous improvements, just-in–time, kaizen, continuous change, and 5S. The production of only what the customer needs without extra work is called pull systems. Continuous improvement refers to continuously improving existing processes. Just-intime refers the time components and materials arrive at the exact place where they are needed. Kaizen refers to continuous improvement. It is achieved through small changes that are made continuously. Finally, 5S stands for sort, set in order, shine, standardize, and sustain. These five elements work together to produce the best results.
The Lean Production System
The lean production system is based on six key concepts:
-
Flow is about moving material and information as near as customers can.
-
Value stream mapping - break down each stage of a process into discrete tasks and create a flowchart of the entire process;
-
Five S's – Sort, Put In Order Shine, Standardize and Sustain
-
Kanban - visual cues such as stickers or colored tape can be used to track inventory.
-
Theory of constraints: identify bottlenecks in your process and eliminate them using lean tools, such as kanban board.
-
Just-in-time - deliver components and materials directly to the point of use;
-
Continuous improvement: Make incremental improvements to the process instead of overhauling it completely.