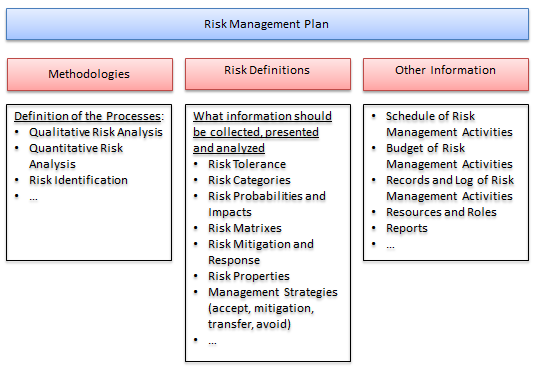
Planning a capacity plan strategy requires you to take into account the expected workload growth, as well as any customer-driven growth. You should then plan accordingly. Here are four common scenarios to consider: Lead, Lag, Match, Adjustment. Each scenario offers different benefits and challenges. To ensure effective capacity planning, you need to consider all of these factors.
Lead strategy
Companies that have a strong strategy for capacity planning can be proactive in expanding capacity, expanding the system, or reducing demand. The lag strategy waits for demand to increase before increasing capacity. The advantage of a leading strategy is that you can avoid running out of capacity due unexpected demand increases.
This strategy can be used in many situations, but it is most effective when the volume of goods or services will be higher than expected. It is also useful when demand is high, like during holidays. Retailers can hire seasonal workers to help them staff their stores for more customers. A lead strategy also allows for quick additions of headcount.
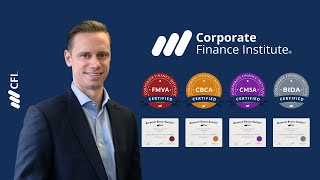
Lag strategy
To match demand and capacity, the Lag strategy is used for capacity planning. While this strategy is more risky than the Lead strategy it does require a lot of work and effort. This strategy is also more risk-averse than either of the other strategies. The lead strategy attempts to anticipate future demands and expand capacity accordingly. This strategy may not be the best for certain organizations due to time and resource constraints.
A lag strategy is a good choice for companies with a stable business model. It prevents wasteful resources and excess inventory by only expanding production when demand for the product increases. This approach can cause stress in the process of training and hiring new employees. A leader strategy, in contrast, is more aggressive. They anticipate future demand and meet those needs before they happen.
Match strategy
The Match strategy serves as a compromise between the Lead- and Lag strategies. It promotes incremental capacity growth, not anticipating increased demand. It is more work to plan and implement, but it is safer for most manufacturers. While it may not be cheap to increase capacity, it is much safer than the two other strategies.
Match strategy is about analyzing forecasts and monitoring current demand. This allows companies to react quickly to changes in the demand. It is more work but it allows for quick and efficient pivots. It also helps streamline operations by ensuring that the resources available are adequate for the current and future demands.
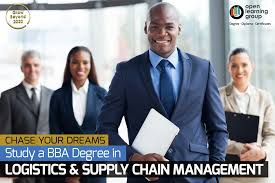
Adjustment strategy
An Adjustment strategy is a common way to manage supply chain capacity. This strategy ensures that supply chains are always available to meet demand. It is also a way for businesses to meet their targets and grow their businesses. The key to maximizing your bottom line is choosing the right strategy. The Adjustment strategy is a way for organizations to better meet their supply chain needs.
It forces organizations and workers to be more realistic about their resource allocations. Overestimating your resources can result in low productivity and low worker motivation. Over-allocating budgets creates significant opportunity costs, as they could have been spent on continuous service improvement, innovation, or employee pay. This strategy makes it more difficult for leaders to forecast their budgets realistically.
FAQ
What is the best way to motivate your employees as a manager?
Motivation is the desire to do well.
You can get motivated by doing something enjoyable.
You can also get motivated by seeing your contribution to the success or the improvement of the organization.
For example, if your goal is to become a physician, you will probably find it more motivational to see patients rather than to read a lot of medicine books.
Another source of motivation is within.
For example, you might have a strong sense of responsibility to help others.
Maybe you like working hard.
Ask yourself why you aren't feeling motivated.
Next, think of ways you can improve your motivation.
Why does it sometimes seem so difficult to make good business decisions?
Complex systems with many moving parts are the hallmark of businesses. They require people to manage multiple priorities and deal with uncertainty and complexity.
Understanding how these factors impact the whole system is key to making informed decisions.
You must first consider what each piece of the system does and why. You then need to consider how those individual pieces interact with each other.
You need to ask yourself if your previous actions have led you to make unfounded assumptions. If they don't, you may want to reconsider them.
Try asking for help from another person if you're still stuck. They may see things differently from you and have insights that could help you find a solution.
What are the most common errors made by managers?
Sometimes managers make their job harder than they need to.
They may not assign enough responsibilities to staff members and provide them with inadequate support.
Additionally, many managers lack communication skills that are necessary to motivate and direct their teams.
Managers can set unrealistic expectations for their employees.
Managers may choose to solve every problem all by themselves, instead of delegating to others.
Statistics
- 100% of the courses are offered online, and no campus visits are required — a big time-saver for you. (online.uc.edu)
- As of 2020, personal bankers or tellers make an average of $32,620 per year, according to the BLS. (wgu.edu)
- The average salary for financial advisors in 2021 is around $60,000 per year, with the top 10% of the profession making more than $111,000 per year. (wgu.edu)
- The BLS says that financial services jobs like banking are expected to grow 4% by 2030, about as fast as the national average. (wgu.edu)
- This field is expected to grow about 7% by 2028, a bit faster than the national average for job growth. (wgu.edu)
External Links
How To
How can Lean Manufacturing be done?
Lean Manufacturing processes are used to reduce waste and improve efficiency through structured methods. They were developed by Toyota Motor Corporation in Japan during the 1980s. It was designed to produce high-quality products at lower prices while maintaining their quality. Lean manufacturing emphasizes removing unnecessary steps from the production process. It consists of five basic elements: pull systems, continuous improvement, just-in-time, kaizen (continuous change), and 5S. Pull systems involve producing only what the customer wants without any extra work. Continuous improvement involves constantly improving upon existing processes. Just-in-time is when components and other materials are delivered at their destination in a timely manner. Kaizen is continuous improvement. This can be achieved by making small, incremental changes every day. Finally, 5S stands for sort, set in order, shine, standardize, and sustain. These five elements work together to produce the best results.
Lean Production System
Six key concepts make up the lean manufacturing system.
-
Flow - focuses on moving information and materials as close to customers as possible.
-
Value stream mapping - Break down each stage in a process into distinct tasks and create an overview of the whole process.
-
Five S’s - Sorted, In Order. Shine. Standardize. And Sustain.
-
Kanban – visual signals like colored tape, stickers or other visual cues are used to keep track inventory.
-
Theory of Constraints - Identify bottlenecks in the process, and eliminate them using lean tools such kanban boards.
-
Just-in time - Get components and materials delivered right at the point of usage;
-
Continuous improvement - incremental improvements are made to the process, not a complete overhaul.