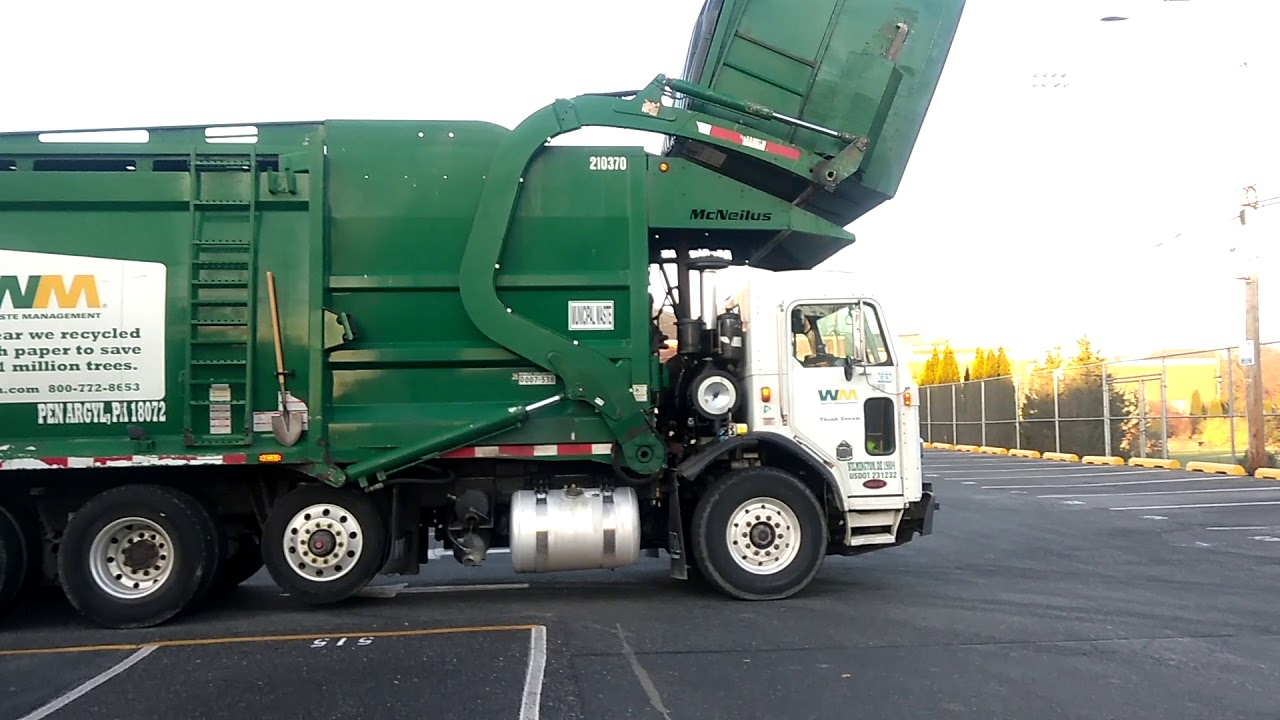
The goal of talent supply chain management is to maximize the supply of talent and the services that are provided by the talent that a company needs. Doing this will allow companies to better produce, distribute, deliver, meet their strategic goals, and more effectively manage their talent supply chain. Read on to learn more about this proactive approach to talent management. In this article, we will explore how this approach can improve your company's human capital management and production processes. We'll also examine how it can help reduce risks associated with contingent employees.
Supply chain of adaptive talent
Building an adaptive talent supply chain is a strategic process for attracting and hiring the best talent for your company. This can balance your workforce and meet your evolving business needs. Employers today face challenges in adapting to changing workforce demographics, a lack of smart skills, or obstacles to staying competitive. Here are some methods to create an adaptive talent supply chain within your organization. First, identify the talent gaps.
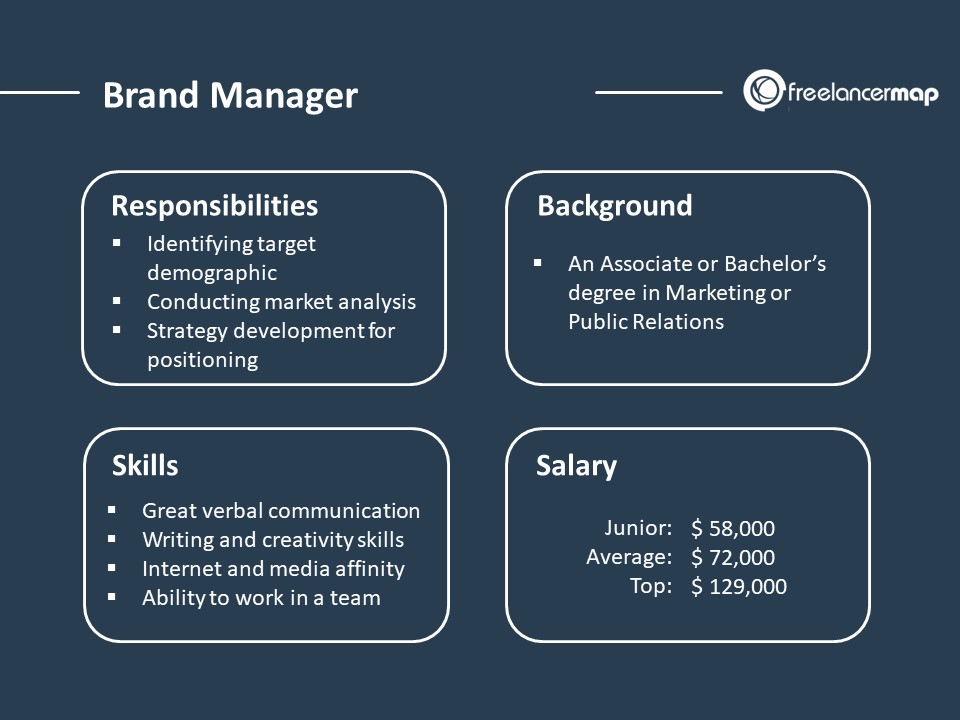
Developing existing talent
For any company, it is vital to nurture existing talent. There are a variety of ways to develop this talent, from formal training to mentoring, and the returns can be very significant. Successful supply chains require companies to continue to develop existing talent. They also need to attract and retain the best employees. This can only happen if the supply chain and human resource functions work together. Although it is an important step in talent management, developing existing talent can be difficult.
Recruting new talent
Employers are finding it increasingly difficult to find qualified workers due to the difficulty in finding them. Commentators often attribute the Great Resignation to an increase in retirement rates and the absence of affordable childcare. However, the root cause of the problem is more structural. A lack of a talent supply chain is one of the reasons for this problem.
Limiting the risk of contingent workers
While there are many advantages to using contingent workers, there are also some risks that organizations need to consider. While employers recognize the benefits of using contingent workers, many aren't prepared to address or mitigate these risks. Ultimately, they need to implement an integrated risk assessment model that takes into account all of the factors that impact contingent labor management. This model should contain processes, contracts and audits that are essential to the successful implementation of a contingent workforce management program.
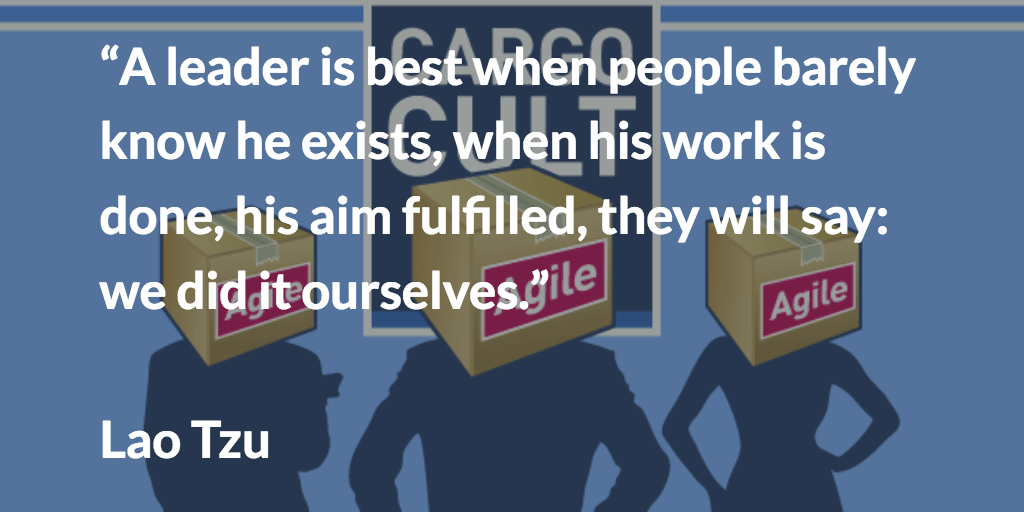
Managing existing talent
Employers should invest in developing existing talent. Competitive advantage for a company is dependent on the skills of its employees. However, in many cases, it is best to leave a company than to progress within it. Turnover is high and many businesses struggle to retain existing employees. Turnover can be prevented by investing in the talent of the workforce the way they would invest in R&D. Training workers does not happen overnight, so companies must invest in training them early on.
FAQ
Why does it sometimes seem so hard to make good business decisions
Complex systems and many moving parts make up businesses. They require people to manage multiple priorities and deal with uncertainty and complexity.
Understanding the impact of these factors on the system is crucial to making sound decisions.
You need to be clear about the roles and responsibilities of each system. You then need to consider how those individual pieces interact with each other.
You should also ask yourself if there are any hidden assumptions behind how you've been doing things. If not, you might want to revisit them.
Asking for assistance from someone else is a good idea if you are still having trouble. They may see things differently from you and have insights that could help you find a solution.
What are the most common errors made by managers?
Managers sometimes make their own job harder than necessary.
They may not delegate enough responsibilities and not provide sufficient support.
Managers often lack the communication skills necessary to motivate and guide their teams.
Managers set unrealistic expectations and make it difficult for their team.
Managers may prefer to solve every problem for themselves than to delegate responsibility.
How do you effectively manage employees?
Achieving employee happiness and productivity is key to managing them effectively.
It means setting clear expectations for them and keeping an eye on their performance.
To do this successfully, managers need to set clear goals for themselves and for their teams.
They should communicate clearly with employees. They also need to make sure that they discipline and reward the best performers.
They must also keep track of the activities of their team. These include:
-
What was achieved?
-
What was the work involved?
-
Who did it all?
-
Was it done?
-
Why it was done?
This information is useful for monitoring performance and evaluating the results.
What role does a manager play in a company?
Each industry has a different role for a manager.
Managers generally oversee the day-today operations of a business.
He/she ensures the company meets its financial commitments and produces goods/services that customers demand.
He/she makes sure that employees adhere to the rules and regulations as well as quality standards.
He/she is responsible for the development of new products and services, as well as overseeing marketing campaigns.
What is Six Sigma?
Six Sigma employs statistical analysis to identify problems, measure them and analyze root causes. Six Sigma also uses experience to correct problems.
The first step is to identify the problem.
Next, data will be collected and analyzed to determine trends and patterns.
The problem is then rectified.
Final analysis of data is done to determine if the problem has been solved.
This continues until the problem has been solved.
What is the difference between TQM and Six Sigma?
The main difference between these two quality management tools is that six sigma focuses on eliminating defects while total quality management (TQM) focuses on improving processes and reducing costs.
Six Sigma is a method for continuous improvement. This method emphasizes eliminating defects using statistical methods such p-charts, control charts, and Pareto analysis.
This method seeks to decrease variation in product output. This is accomplished by identifying the root cause of problems and fixing them.
Total Quality Management involves monitoring and measuring every aspect of the organization. It also involves training employees to improve performance.
It is frequently used as an approach to increasing productivity.
Statistics
- Our program is 100% engineered for your success. (online.uc.edu)
- The profession is expected to grow 7% by 2028, a bit faster than the national average. (wgu.edu)
- The average salary for financial advisors in 2021 is around $60,000 per year, with the top 10% of the profession making more than $111,000 per year. (wgu.edu)
- Hire the top business lawyers and save up to 60% on legal fees (upcounsel.com)
- This field is expected to grow about 7% by 2028, a bit faster than the national average for job growth. (wgu.edu)
External Links
How To
How does Lean Manufacturing work?
Lean Manufacturing methods are used to reduce waste through structured processes. They were developed by Toyota Motor Corporation in Japan during the 1980s. The main goal was to produce products at lower costs while maintaining quality. Lean manufacturing emphasizes removing unnecessary steps from the production process. It is composed of five fundamental elements: continuous improvement; pull systems, continuous improvements, just-in–time, kaizen, continuous change, and 5S. It is a system that produces only the product the customer requests without additional work. Continuous improvement is the continuous improvement of existing processes. Just-in–time refers when components or materials are delivered immediately to their intended destination. Kaizen is continuous improvement. This can be achieved by making small, incremental changes every day. Five-S stands for sort. It is also the acronym for shine, standardize (standardize), and sustain. To achieve the best results, these five elements must be used together.
Lean Production System
Six key concepts make up the lean manufacturing system.
-
Flow - The focus is on moving information and material as close as possible to customers.
-
Value stream mapping is the ability to divide a process into smaller tasks, and then create a flowchart that shows the entire process.
-
Five S's: Sort, Shine Standardize, Sustain, Set In Order, Shine and Shine
-
Kanban – visual signals like colored tape, stickers or other visual cues are used to keep track inventory.
-
Theory of constraints: Identify bottlenecks and use lean tools such as kanban boards to eliminate them.
-
Just-in Time - Send components and material directly to the point-of-use;
-
Continuous improvement is making incremental improvements to your process, rather than trying to overhaul it all at once.