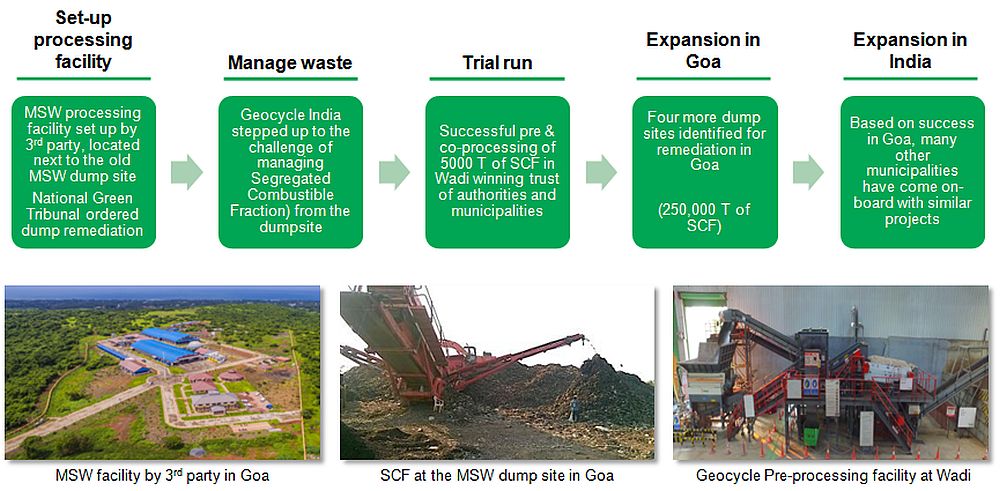
Engineering a building can be a complicated process. There are many kinds of engineers who work in the construction industry. There are many types of engineers working in the construction industry: there are Fire protection engineers, Civil engineers, Structural engineering engineers, and electrical engineers. These engineers develop construction plans from scratch and supervise the execution of these plans. They may also work with manual labor and other engineers. As energy-efficient buildings become increasingly important to clients, engineers are often asked to propose alternative methods of generating power. Using solar energy, for example, is a common method for this process.
Civil engineers
A civil engineer is a professional involved in construction projects. They are responsible for planning, designing, and constructing projects. In addition, they also test the final products to ensure that they work as expected. They spend much of their time on-site, dealing with many challenges and keeping pace with the progress. Their primary goal, however, is to construct a structure that's safe and environmentally friendly. Many people want to be civil engineers and are looking for a career.
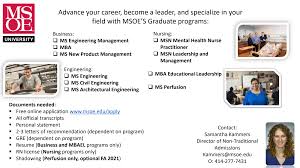
Structural engineers
It is not always clear what role structural engineers play in construction. The role includes the analysis of basic building components and liaison with other members of project teams. Monitoring and inspecting work being done by contractors is another part of the job. This may include the assessment of the foundations' properties and conditions. The computer-aided modeling (CAD) technology is also used by structural engineers to ensure that buildings are constructed correctly.
Electrical engineers
An electrical engineer in a construction site plays a key role in ensuring maximum safety on the job. They ensure electrical appliances are safe for workers and there are no exposed connections. They make sure that high-risk areas are not available. This job requires excellent time management skills and communication skills. All technical and soft skills are required to ensure safety on construction sites. They must also be familiar with electrical safety codes and regulations.
Fire protection engineers
The chemistry and materials used in buildings are essential for fire protection engineers. They must also be familiar with the interactions between fire-fighting chemicals and suppression chemicals. They must also work closely with public and legal enforcement. They must be familiar with the correct procedures for creating court documents, presenting findings and conducting studies. It is possible to obtain a Master of Science, but it is not essential. Research in academia requires only a doctorate. There are many schools that offer fire protection engineering certification.
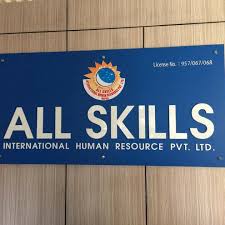
Environmental engineers
The construction industry is one of the largest end users of natural resources and the largest source of pollutants. Environmental engineers' role is to improve the sustainability and performance of the construction industry. By employing life cycle assessments and innovative design, environmental engineers can optimize construction sites and minimize impacts on the environment. Environmental engineers can help change outdated practices into environmentally friendly methods. Their expertise will be critical to the future development of the construction sector. Here are the main roles of environmental engineers.
FAQ
What's the difference between Six Sigma and TQM?
The main difference in these two quality management tools lies in the fact that six sigma is focused on eliminating defects and total quality management (TQM), emphasizes improving processes and reducing costs.
Six Sigma can be described as a strategy for continuous improvement. It emphasizes the elimination or minimization of defects through statistical methods such control charts and p charts.
This method attempts to reduce variations in product output. This is accomplished through identifying and correcting root causes.
Total quality management refers to the monitoring and measurement of all aspects in an organization. It also includes training employees to improve performance.
It is often used to increase productivity.
What are the steps that management takes to reach a decision?
The decision-making process of managers is complicated and multifaceted. This involves many factors including analysis, strategy and planning, implementation, measurement and evaluation, feedback, feedback, and others.
When managing people, the most important thing to remember is that they are just human beings like you and make mistakes. You can always improve your performance, provided you are willing to make the effort.
This video will explain how decision-making works in Management. We will explain the importance of different types decisions and how every manager can make them. You'll learn about the following topics:
What is the best way to motivate your employees as a manager?
Motivation refers to the desire to perform well.
Engaging in something fun can be a great way to get motivated.
Or you can get motivated by seeing yourself making a contribution to the success of the organization.
For example, if you want to become a doctor, you'll probably find it more motivating to see patients than to study medicine books all day.
The inner motivation is another type.
Perhaps you have a strong sense to give back, for example.
Or you might enjoy working hard.
If you feel unmotivated, ask yourself why.
Then, consider ways you could improve your motivation.
Why is it so hard to make smart business decisions?
Complex systems and many moving parts make up businesses. People who manage them have to balance multiple priorities while dealing with complexity and uncertainty.
Understanding the impact of these factors on the system is crucial to making sound decisions.
You need to be clear about the roles and responsibilities of each system. Then, you need to think about how these pieces interact with one another.
You need to ask yourself if your previous actions have led you to make unfounded assumptions. If so, it might be worth reexamining them.
If you're still stuck after all this, try asking someone else for help. You might find their perspective is different from yours and they may have insight that can help you find the solution.
Statistics
- Your choice in Step 5 may very likely be the same or similar to the alternative you placed at the top of your list at the end of Step 4. (umassd.edu)
- This field is expected to grow about 7% by 2028, a bit faster than the national average for job growth. (wgu.edu)
- As of 2020, personal bankers or tellers make an average of $32,620 per year, according to the BLS. (wgu.edu)
- The average salary for financial advisors in 2021 is around $60,000 per year, with the top 10% of the profession making more than $111,000 per year. (wgu.edu)
- 100% of the courses are offered online, and no campus visits are required — a big time-saver for you. (online.uc.edu)
External Links
How To
How does Lean Manufacturing work?
Lean Manufacturing is a method to reduce waste and increase efficiency using structured methods. They were developed by Toyota Motor Corporation in Japan during the 1980s. The primary goal was to make products with lower costs and maintain high quality. Lean manufacturing seeks to eliminate unnecessary steps and activities in the production process. It has five components: continuous improvement and pull systems; just-in time; continuous change; and kaizen (continuous innovation). Pull systems allow customers to get exactly what they want without having to do extra work. Continuous improvement means continuously improving on existing processes. Just-in-time is when components and other materials are delivered at their destination in a timely manner. Kaizen refers to continuous improvement. It is achieved through small changes that are made continuously. Last but not least, 5S is for sort. These five elements are used together to ensure the best possible results.
Lean Production System
Six key concepts are the basis of lean production:
-
Flow - focuses on moving information and materials as close to customers as possible.
-
Value stream mapping is the ability to divide a process into smaller tasks, and then create a flowchart that shows the entire process.
-
Five S's: Sort, Shine Standardize, Sustain, Set In Order, Shine and Shine
-
Kanban - visual cues such as stickers or colored tape can be used to track inventory.
-
Theory of constraints: Identify bottlenecks and use lean tools such as kanban boards to eliminate them.
-
Just-in-time delivery - Deliver components and materials right to your point of use.
-
Continuous improvement - Make incremental improvements rather than overhauling the entire process.