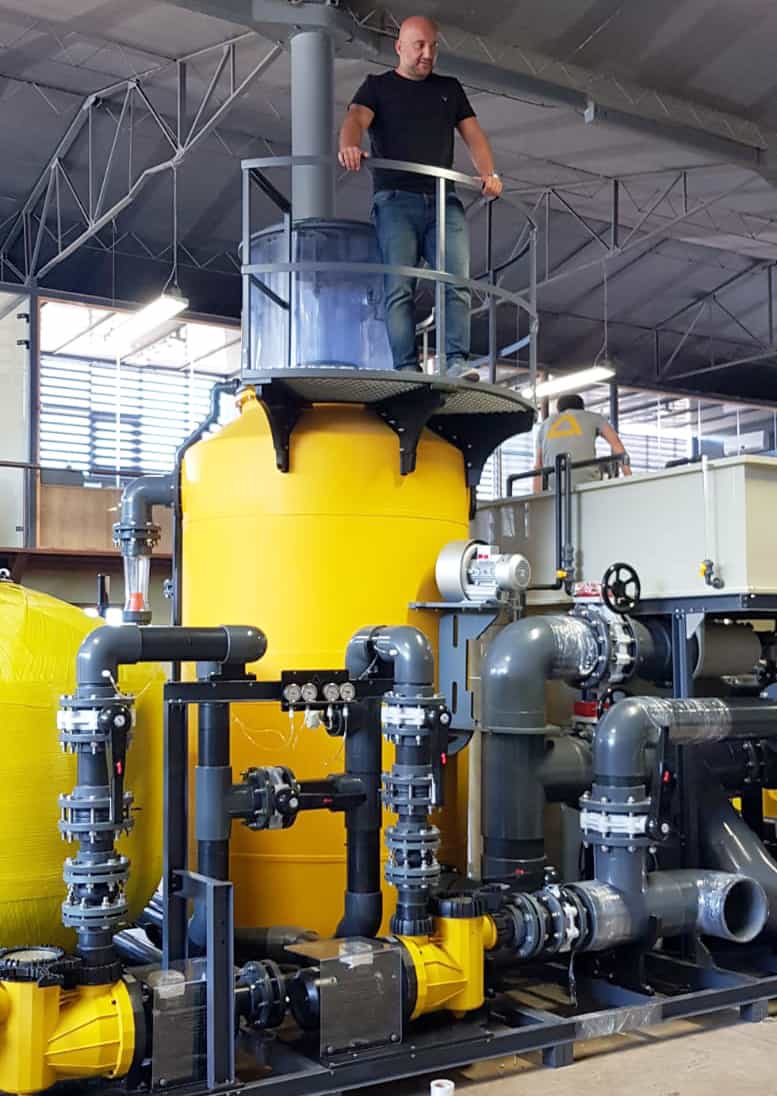
The aim of a construction planning and scheduling course is to improve the working knowledge of students in this field and train them to be professional construction managers. Students will get the necessary training and education to succeed in the construction industry. Students will learn cost control and resource leveling as well as the use of construction schedules, computer-based plan software, and the practical application of these tools. This course will help you reach your goals, regardless of whether you are interested in setting up a construction business or working in an established company.
Bar chart
Bar charts are a common form of project representation in construction. It is particularly useful for communicating status information. However, it is important to remember that changes in the schedule of one activity will require changes in the schedules of its successors. To indicate precedence, many schemes have been designed to link activity bars mechanically. You can also use computer-based tools to represent precedence relationships.
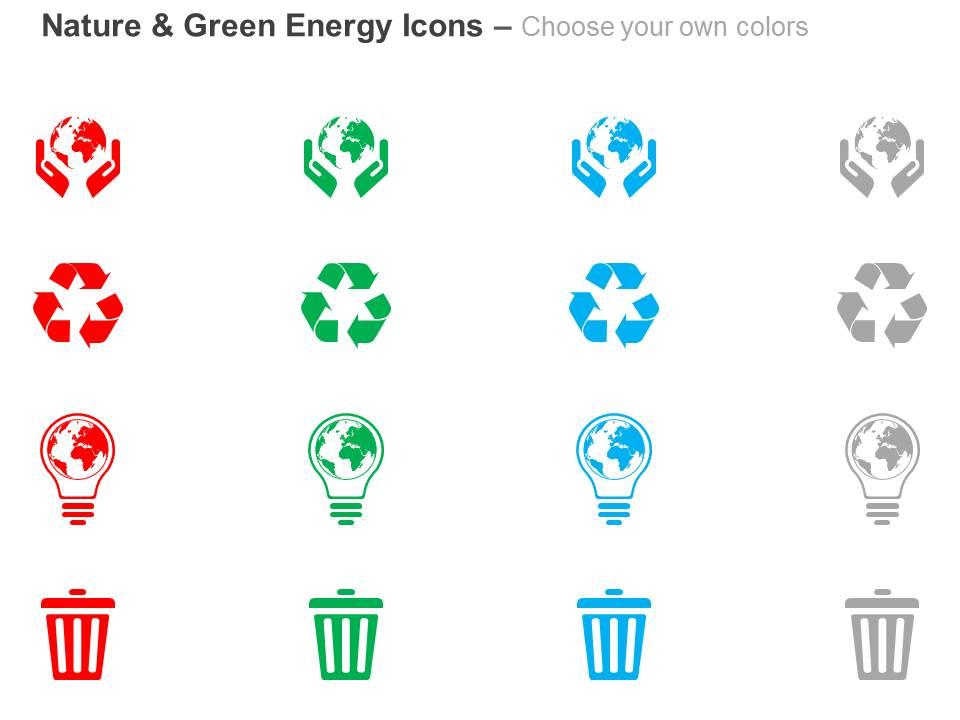
Gantt chart
Gantt charts are essential tools in construction planning and scheduling. It allows you to plan more efficiently and helps you keep track on the project's progress. Gantt diagrams are useful for many purposes, such as planning meetings or involving multiple skill sets. It is simple to read and can be used to track the progress of a project. Learn more about the Gantt charts in our construction planning and scheduling courses.
Diagrams showing Activity Precedence
You might be interested in project scheduling if you have completed an activity precedence diagrams course at college. The fundamental difference between precedence and Arrow diagramming is the fact that both allow all types of relationships. Arrow diagrams are based on the finish to begin relationship. Precedence diagrams limit the number of arrows between elements. An arrow chart shows an activity as an icon with an outline. A precedence map uses boxes or nodes for the activities. The length of an arrow is the duration of the activity, while a blank space means nothing.
PERT
These courses provide an overview of the principles and practices involved in scheduling and planning complex construction projects. Gantt charts will be covered as well as network scheduling, PERT and Critical Path Methods, linear scheduling, earned value analysis, Gantt charts, and Gantt charts. The principles will be applied in simulated construction projects. Each assessment must be completed at least 40% to pass the course. The course takes approximately 700 to 800 hours. An electronic certificate of completion will be sent to you after you complete the course.

Employee scheduling
If you are interested in learning about construction projects, construction planning and scheduling courses will help you to develop these skills. These courses cover topics like critical path planning, the critical path method and time and resource allocation as well as project costing. Additionally, the courses cover industry best practices as well as group planning methods. These are just a few of the many benefits to taking these classes. Once you complete these courses, your knowledge and skills will allow you to take on any type or construction project.
FAQ
How can a manager motivate employees?
Motivation refers to the desire to perform well.
Enjoyable activities can motivate you.
You can also get motivated by seeing your contribution to the success or the improvement of the organization.
If you are a doctor and want to be one, it will likely be more rewarding to see patients than to read medical books every day.
Motivation comes from within.
One example is a strong sense that you are responsible for helping others.
Maybe you like working hard.
If you feel unmotivated, ask yourself why.
Then try to think about ways to change your situation to be more motivated.
What are the main management skills?
No matter if they are running a local business or an international one, management skills are vital. These include the ability and willingness to manage people, finances as well resources, time and space.
You will need management skills to set goals and objectives, plan strategies, motivate employees, resolve problems, create policies and procedures, and manage change.
As you can see, there's no end to the list of managerial duties!
What does Six Sigma mean?
Six Sigma uses statistics to measure problems, find root causes, fix them, and learn from past mistakes.
First, identify the problem.
The next step is to collect data and analyze it in order to identify trends or patterns.
Then corrective actions are taken to solve the problem.
Finally, data will be reanalyzed to determine if there is an issue.
This cycle continues until the problem is solved.
What is Six Sigma?
It is a way to improve quality that places emphasis on customer service and continuous learning. The goal is to eliminate defects by using statistical techniques.
Motorola created Six Sigma as part of their efforts to improve manufacturing processes in 1986.
This idea quickly spread throughout the industry. Today, many organizations use six sigma methods for product design, production and delivery.
What's the difference between Six Sigma and TQM?
The main difference in these two quality management tools lies in the fact that six sigma is focused on eliminating defects and total quality management (TQM), emphasizes improving processes and reducing costs.
Six Sigma is a methodology for continuous improvement. It emphasizes the elimination of defects by using statistical methods such as control charts, p-charts, and Pareto analysis.
This method has the goal to reduce variation of product output. This is accomplished through identifying and correcting root causes.
Total Quality Management involves monitoring and measuring every aspect of the organization. It also involves training employees to improve performance.
It is frequently used as an approach to increasing productivity.
Statistics
- This field is expected to grow about 7% by 2028, a bit faster than the national average for job growth. (wgu.edu)
- As of 2020, personal bankers or tellers make an average of $32,620 per year, according to the BLS. (wgu.edu)
- Hire the top business lawyers and save up to 60% on legal fees (upcounsel.com)
- UpCounsel accepts only the top 5 percent of lawyers on its site. (upcounsel.com)
- The profession is expected to grow 7% by 2028, a bit faster than the national average. (wgu.edu)
External Links
How To
What are the 5S for the workplace?
Your first step in making your workplace more efficient and productive is to organize everything. An organized workspace, clean desk and tidy room will make everyone more productive. To ensure space is efficiently used, the five S's (Sort Shine, Sweep Separate, Store and Separate) are all essential. In this session, we'll go through these steps one at a time and see how they can be implemented in any type of environment.
-
Sort. Don't waste your time looking for things you already know are there. You need to put your things where you use them the most. You should keep it close to the area where you research or look up information. Also, consider whether you really need it. If it isn't useful, get rid!
-
Shine. You should get rid of any items that could be harmful or cause injury to others. It is possible to have too many pens around and not be able to safely store them. A pen holder is a great investment as you won't lose your pens.
-
Sweep. Clean off surfaces regularly to prevent dirt from building up on your furniture and other items. You may want to invest in some dusting equipment to ensure that all surfaces are as clean as possible. To keep your workspace tidy, you could even designate a particular area for dusting and cleaning.
-
Separate. When you are ready to dispose off your trash, it is a good idea to separate it into bins. Trash cans are placed in strategic locations throughout the office so you can quickly dispose of garbage without having to search for it. You can take advantage of this location and place trash bags near each bin to make it easy to find what you are looking for.