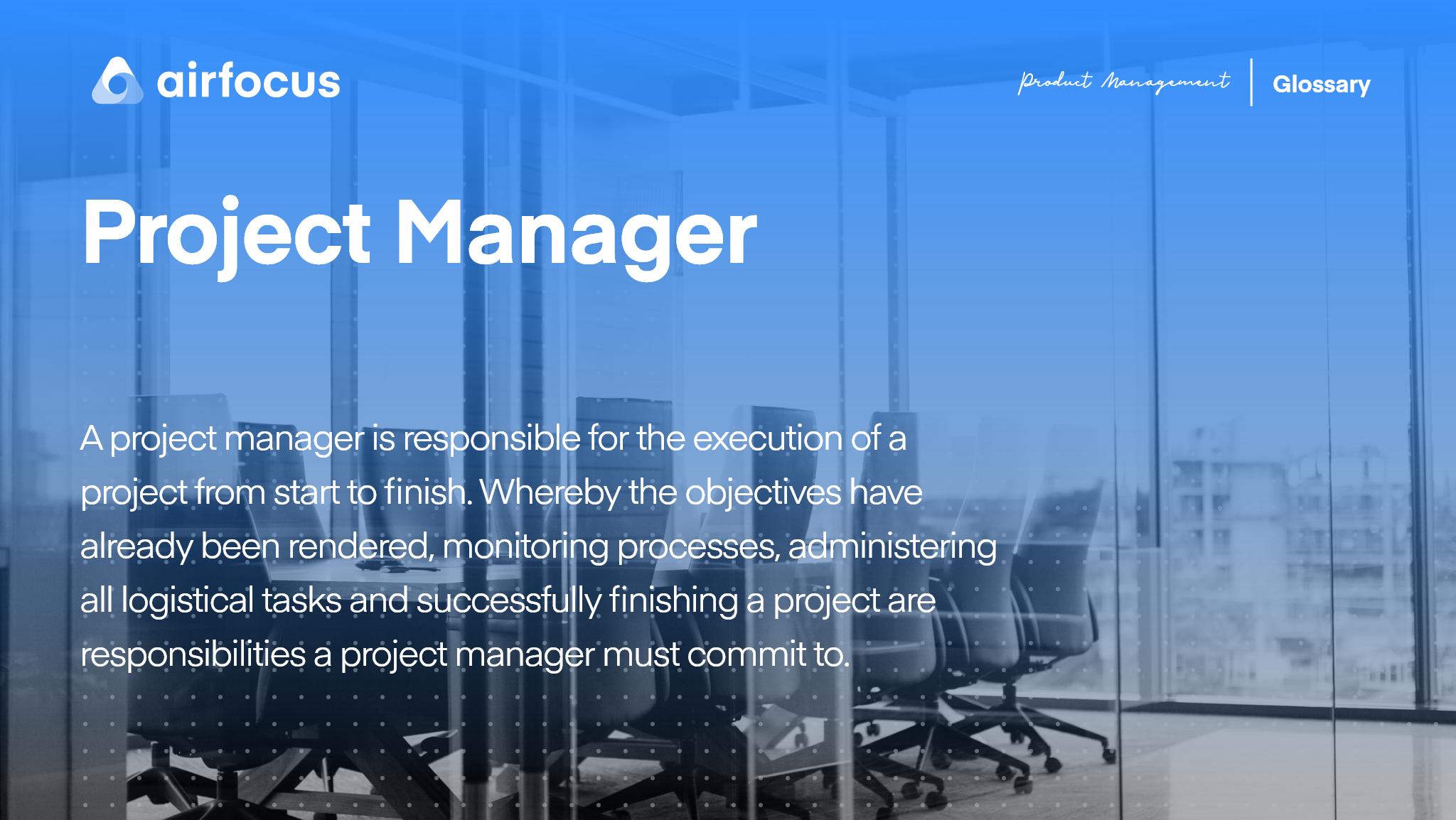
To ensure the safety of your workers, it is vital to implement proper fall protection safety measures. Inspections, training, and maintenance are all important. Not only should workers be equipped with the proper equipment, but fall protection safety precautions must also address hazards and remove them. Continue reading to learn more about fall safety. We hope you have found the right information in this article.
Training is important for fall protection safety
Fall protection safety training is crucial, especially for those who work at heights. Training in fall protection is essential for both safety officers as well as environmental health professionals. An adequately trained individual can help identify potential hazards and recommend the best solutions. Training may include instruction in emergency procedures and the selection of appropriate safety equipment.
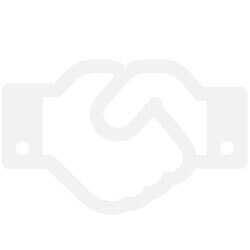
Training in fall protection can be done via lectures, videos, and online courses. These courses do lack the hands-on aspect that is necessary for fall protection safety. Training in-house by a competent person is the best.
Maintenance
Regular inspections and maintenance are essential to maintain your fall protection safety equipment. This will extend the life of your fall protection equipment, and can make your workplace safer. You can have your equipment checked by qualified personnel in France and the Netherlands. You can have your fall protection equipment inspected in Belgium by the External Service for Technical Controls. These inspections are mandatory for fall protection safety equipment, so it's important to get your equipment checked regularly.
It is important to inspect fall protection safety equipment before it is used. If equipment is in poor condition, it should be thrown away and replaced. Before each use, a trained person should inspect the fall protection equipment.
Hazard elimination
Fall protection safety is a top priority. Hazard elimination is one of its most important strategies. This involves identifying the root cause of the falls and then deciding a course to eliminate the risk. Most cases, this means making changes to equipment, practice, or location that eliminate the danger. To reduce the chance of falling, you can install HVAC equipment on the ground and not in an equipment room. To reduce the likelihood of falling, another fall prevention strategy is to change lighting fixtures.
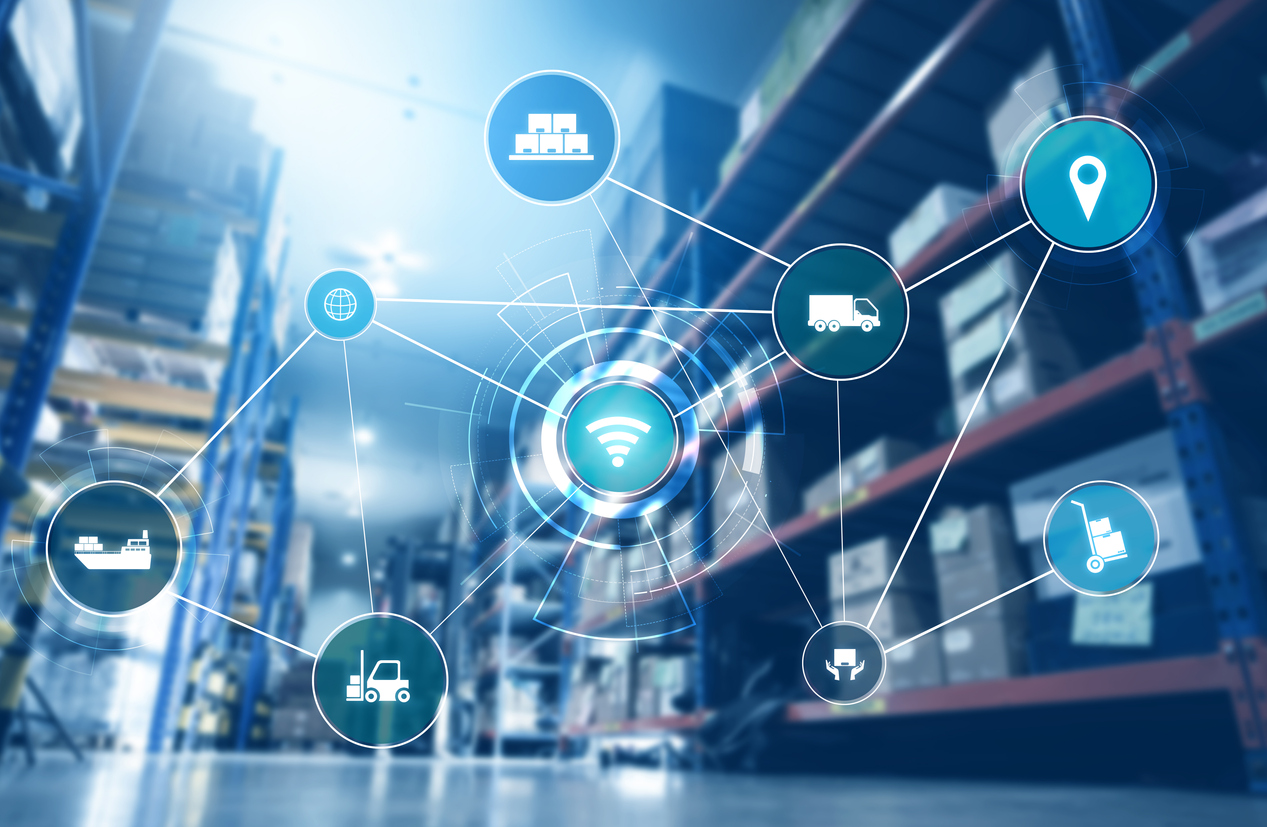
The company should also develop a rescue plan. This plan should detail the steps and procedures to use if someone falls. A fall prevention plan should also address hazards unique to the work environment.
FAQ
How does a manager motivate his/her employees?
Motivation is the desire to do well.
Enjoyable activities can motivate you.
Another way to get motivated is to see yourself as a contributor to the success of the company.
If you are a doctor and want to be one, it will likely be more rewarding to see patients than to read medical books every day.
A different type of motivation comes directly from the inside.
You might feel a strong sense for responsibility and want to help others.
Perhaps you enjoy working hard.
If you don’t feel motivated, find out why.
Then think about how you can make your life more motivating.
Which kind of people use Six Sigma
Six sigma is a common concept for people who have worked in statistics or operations research. Anybody involved in any aspect or business can benefit.
Because it requires a high degree of commitment, only leaders with strong leadership skills can implement it successfully.
How can we make our company culture successful?
A culture of respect and value within a company is key to a productive culture.
It's based on three main principles:
-
Everybody has something of value to share
-
People are treated with respect
-
People and groups should respect each other.
These values are reflected by the way people behave. They will treat others with kindness and consideration.
They will listen respectfully to the opinions of others.
They can also be a source of inspiration for others.
A company culture encourages collaboration and communication.
People feel free to express their views openly without fear of reprisal.
They know that they will not be judged if they make mistakes, as long as the matter is dealt with honestly.
Finally, the company culture promotes honesty and integrity.
Everyone understands that the truth is always best.
Everyone knows that there are rules and regulations that apply to them.
And no one expects special treatment or favors.
What is Six Sigma?
It's a strategy for quality improvement that emphasizes customer care and continuous learning. The goal is to eliminate defects by using statistical techniques.
Six Sigma was developed at Motorola in 1986 as part of its efforts to improve manufacturing processes.
The idea spread quickly throughout the industry, and today, many organizations are using six sigma methods to improve product design, production, delivery, and customer service.
What are the most common errors made by managers?
Sometimes managers make their job harder than they need to.
They may not delegate enough responsibilities to staff and fail to give them adequate support.
Managers often lack the communication skills necessary to motivate and guide their teams.
Managers sometimes set unrealistic expectations of their teams.
Managers may prefer to solve every problem for themselves than to delegate responsibility.
Why is project management so important?
Project management techniques can be used to ensure smooth project execution and meeting deadlines.
This is because many businesses depend heavily upon project work to produce products and services.
These projects must be managed efficiently and effectively by companies.
Companies can lose time, money, and reputation if they don't have a good project management system.
Statistics
- The profession is expected to grow 7% by 2028, a bit faster than the national average. (wgu.edu)
- UpCounsel accepts only the top 5 percent of lawyers on its site. (upcounsel.com)
- Your choice in Step 5 may very likely be the same or similar to the alternative you placed at the top of your list at the end of Step 4. (umassd.edu)
- This field is expected to grow about 7% by 2028, a bit faster than the national average for job growth. (wgu.edu)
- Our program is 100% engineered for your success. (online.uc.edu)
External Links
How To
How do you implement a Quality Management Plan (QMP)?
QMP (Quality Management Plan) is a system to improve products and services by implementing continuous improvement. It is about how to continually measure, analyze, control, improve, and maintain customer satisfaction.
QMP stands for Quality Management Process. It is used to guarantee good business performance. QMP's goal is to improve service delivery and production. A QMP should include all three aspects - Processes, Products, and Services. The QMP that only addresses one aspect of the process is called a Process QMP. When the QMP focuses on a Product/Service, it is known as a "Product" QMP. QMP is also used to refer to QMPs that focus on customer relations.
Two main elements are required for the implementation of a QMP. They are Scope and Strategy. These elements can be defined as follows.
Scope: This describes the scope and duration for the QMP. This scope can be used to determine activities for the first six-months of implementation of a QMP in your company.
Strategy: This describes how you will achieve the goals in your scope.
A typical QMP comprises five phases: Planning and Design, Development, Construction, Implementation, Maintenance. Below is a description of each phase:
Planning: This stage identifies and prioritizes the QMP's objectives. To understand the expectations and requirements of all stakeholders, the project is consulted. Next, you will need to identify the objectives and priorities. The strategy for achieving them is developed.
Design: This stage involves the creation of the vision, mission, strategies and tactics necessary to implement the QMP successfully. These strategies are put into action by developing detailed plans and procedures.
Development: The development team is responsible for building the resources and capabilities necessary to implement the QMP effectively.
Implementation is the actual implementation of QMP according to the plans.
Maintenance: The maintenance of the QMP is an ongoing task.
The QMP must also include several other items:
Participation of Stakeholders: The QMP's success depends on the participation of stakeholders. They should actively be involved during the planning and development, implementation, maintenance, and design stages of QMP.
Project Initiation: It is essential to have a clear understanding about the problem and the solution before you can initiate a project. In other words, they must understand the motivation for initiating the project and the expectations of the outcome.
Time frame: It is crucial to know the time frame for the QMP. The simplest version can be used if the QMP is only being implemented for a short time. However, if you have a long-term commitment, you may require more elaborate versions.
Cost Estimation: Another important component of the QMP is cost estimation. Planning is not possible without knowing the amount of money you will spend. The QMP should be cost-estimated before it can begin.
QMPs should not be considered a static document. It is constantly changing as the company changes. It is important to review it periodically to ensure it meets all current requirements.